Method for separating nano-particles at water-phase density gradient centrifugation rate
A nanoparticle and gradient centrifugation technology, which is applied in solid separation, wet separation, chemical instruments and methods, etc. The effect of wide size range, good separation effect and simple process
- Summary
- Abstract
- Description
- Claims
- Application Information
AI Technical Summary
Problems solved by technology
Method used
Image
Examples
Embodiment 1
[0045] (1) First, 0.1 mg of Au nanoparticle suspension containing 5nm, 10nm and 20nm was added to mercapto-polyethylene glycol 5000 aqueous solution, ultrasonically dispersed, and then concentrated to reduce its volume to 0.2ml.
[0046](2) Make a density gradient: dilute with 60% iodixanol (density 1.32 g / ml) solution by mass percentage to prepare 30%, 40%, and 50% iodixanol solutions respectively. Take 0.75ml each to prepare a density gradient solution of 30%+40%+50%+60%.
[0047] (3) Slowly add 0.2 ml of mixed Au colloidal nanoparticle solution onto the density gradient solution.
[0048] (4) High-speed centrifugation at 15°C, 50,000 rpm, and 15 minutes.
[0049] (5) Take out the centrifuged colloidal nano-dispersion from the top in equal volumes in batches (100ul / time, marked as fn in turn). Finally, Au nanoparticles with different sizes were obtained.
[0050] For separation results, see figure 2 , 3. Similar effects can be achieved by using sucrose, albumin, glycer...
Embodiment 2
[0052] (1) First, about 0.5 mg of 4 nm FeCo@C nanoparticles were ultrasonically dispersed in 5 ml of phospholipid-methylpolyethylene glycol 5000 surfactant solution with a concentration of 1 mg / ml to form 0.1 mg / ml FeCo@C colloids Nanoparticle solution.
[0053] (2) Make density gradient: dilute with 60% iodixanol (density 1.32g / ml) solution by mass percentage to prepare 10%, 20%, 30%, 40% iodixanol solutions respectively. Take 0.75ml each to prepare a density gradient solution of 10%+20%+30%+40%.
[0054] (3) Slowly add 0.2ml FeCo@C colloidal nanoparticle solution to the density gradient solution.
[0055] (4) High-speed centrifugation at 10°C, 45,000 rpm, and 210 minutes.
[0056] (5) Take out the centrifuged colloidal nano-dispersion from the top in equal volumes in batches (100ul / time, marked as fn in turn). Finally, FeCo@C nanoparticles with different sizes were obtained.
[0057] For separation results, see Figure 4 . Similar effects can be achieved by using album...
Embodiment 3
[0059] (1) First, graphite oxide is ultrasonicated in water to prepare a solution of about 2 mg / ml graphene oxide colloidal nanoparticles.
[0060] (2) Make a density gradient: first make a sucrose solution with a mass percentage of 70% (density of 1.34g / ml), then dilute the 70% sucrose solution to prepare 20%, 30%, 40%, 50%, 60% % sucrose solution. Take 0.5ml each to prepare a density gradient solution of 20%+30%+40%+50%+60%+70%.
[0061] (3) Slowly add 0.2ml graphene oxide colloidal nanoparticle solution to the density gradient solution.
[0062] (4) High-speed centrifugation at 15°C, 50,000 rpm, and 15 minutes.
[0063] (5) Take out the centrifuged colloidal nano-dispersion from the top in equal volumes in batches (100ul / time, marked as fn in turn). Finally, graphene oxide with different sizes is obtained.
[0064] For separation results, see Figure 5 . Similar effects can be achieved by using albumin, glycerol, sorbitol, meglumine, and iodixanol solutions with the s...
PUM
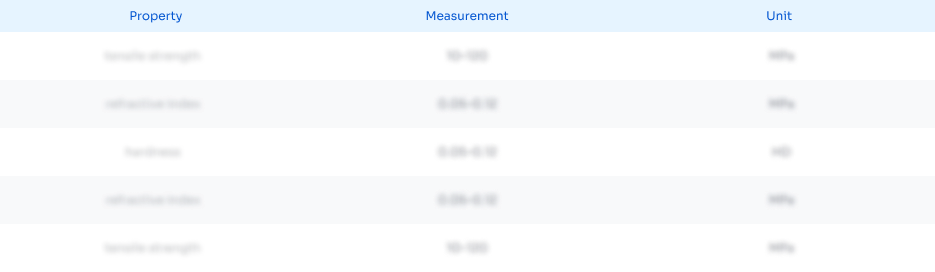
Abstract
Description
Claims
Application Information

- R&D
- Intellectual Property
- Life Sciences
- Materials
- Tech Scout
- Unparalleled Data Quality
- Higher Quality Content
- 60% Fewer Hallucinations
Browse by: Latest US Patents, China's latest patents, Technical Efficacy Thesaurus, Application Domain, Technology Topic, Popular Technical Reports.
© 2025 PatSnap. All rights reserved.Legal|Privacy policy|Modern Slavery Act Transparency Statement|Sitemap|About US| Contact US: help@patsnap.com