Production method for secondary acid hydrolysis of dimethyl ester glyphoate acid
A technology of glyphosate acid, dimethyl ester method, applied in chemical instruments and methods, botanical equipment and methods, biocides, etc., can solve problems such as waste of steam energy, consumption of heat, prolongation of hydrolysis reaction time, etc., to save energy The effect of steam consumption, improving utilization, and reducing cooling consumption
- Summary
- Abstract
- Description
- Claims
- Application Information
AI Technical Summary
Problems solved by technology
Method used
Examples
Embodiment 1
[0031] In a 1L four-neck flask, add 588g of condensation liquid, add 325g of 31% hydrochloric acid at one time, carry out temperature programming, and the reaction is completed in 6 hours, cool and add alkali to adjust the pH to 1.0, crystallize for 8 hours, and obtain solid grass after suction filtration and drying. Glydronic acid 105.2g, dry powder yield 75.1%, total yield 82%.
Embodiment 2
[0033]In a 1L four-neck flask, add 588g of condensation liquid, add 205g of 31% hydrochloric acid for the first time, and carry out temperature program, and the temperature rises to 105°C in 120 minutes. Carry out reflux operation, crystallization occurs after reflux for 90 minutes, stop reflux, continue to heat up to 117°C, add water to lower the temperature to 112°C, keep warm for 20 minutes, and the reaction ends. The total reaction time is 5 hours. Cool and add alkali to adjust the pH to 1.0, crystallize for 8 hours, obtain 105.7 g of solid glyphosate acid after suction filtration and drying, the dry powder yield is 75.5%, and the total yield is 81.3%.
Embodiment 3
[0035] In a 1L four-neck flask, add 705g of condensation liquid, add 275g of 31% hydrochloric acid for the first time, and carry out temperature program, and the temperature rises to 105°C in 120 minutes. Carry out reflux operation, crystallization occurs after reflux for 90 minutes, stop reflux, continue to heat up to 117°C, add water to lower the temperature to 112°C, keep warm for 20 minutes, and the reaction ends. The total reaction time is 5 hours. Cool and add alkali to adjust the pH to 1.0, crystallize for 8 hours, obtain 128.1 g of solid glyphosate acid after suction filtration and drying, the dry powder yield is 77.2%, and the total yield is 82.5%.
PUM
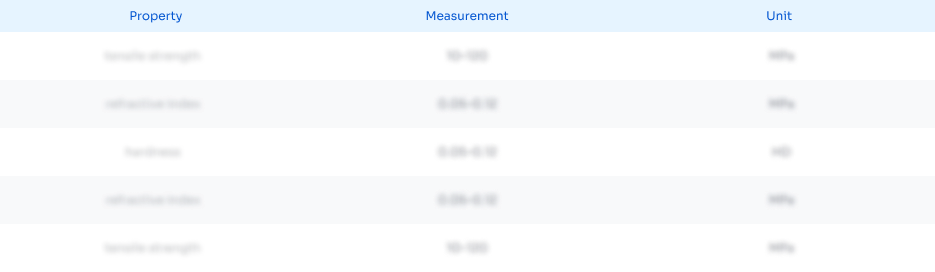
Abstract
Description
Claims
Application Information

- R&D
- Intellectual Property
- Life Sciences
- Materials
- Tech Scout
- Unparalleled Data Quality
- Higher Quality Content
- 60% Fewer Hallucinations
Browse by: Latest US Patents, China's latest patents, Technical Efficacy Thesaurus, Application Domain, Technology Topic, Popular Technical Reports.
© 2025 PatSnap. All rights reserved.Legal|Privacy policy|Modern Slavery Act Transparency Statement|Sitemap|About US| Contact US: help@patsnap.com