Submerged arc bead welding technique
A submerged arc welding and technical technology, applied in the field of surfacing, can solve the problems of insufficient high temperature resistance, affecting production, adhesion, etc., and achieve the effect of improving product production quality and saving production costs
- Summary
- Abstract
- Description
- Claims
- Application Information
AI Technical Summary
Problems solved by technology
Method used
Examples
Embodiment 1
[0016] A submerged arc welding surfacing welding technology, comprising the steps of:
[0017] (1) Reduce the outer surface of the idler roller by 8cm;
[0018] (2) Remove the fatigue layer, defects and cracks on the surface of the roller;
[0019] (3) The idler roller is first heated to 100°C at a rate of 20°C / h, and then preheated to 250°C at a rate of 40°C / h;
[0020] (4) Under the conditions of welding voltage of 20V, welding current of 900A and welding speed of 70mm / min, NH-69S is used as the welding material, and the angular velocity of the supporting roller is controlled to be 15rad / s for rotational welding ;
[0021] (5) Cool the welded idler roll to 100°C and keep it warm for 20 minutes, then continue cooling to below 50°C, and then no longer control the cooling speed;
[0022] (6) Keep the idler roller obtained in the above steps at a tempering temperature of 450° C. for 5 hours;
[0023] (7) Finally, slowly cool the tempered idler rollers to 150°C with the furna...
Embodiment 2
[0025] A submerged arc welding surfacing welding technology, comprising the steps of:
[0026] (1) Reduce the outer surface of the roller by 10cm;
[0027] (2) Remove the fatigue layer, defects and cracks on the surface of the roller;
[0028] (3) Raise the idler roller to 100°C at a speed of 20°C / h, and then preheat at a speed of 40°C / h to make the temperature reach 300°C;
[0029] (4) Under the conditions of welding voltage 30V, welding current 1000A, welding speed 80mm / min, NH-69S is used as welding material, and the angular speed of the idler is controlled at 20rad / s for rotational welding ;
[0030] (5) Cool the welded idler roller to 100°C and keep it warm for 30 minutes, then continue cooling to below 50°C, and then no longer control the cooling speed;
[0031] (6) Keep the idler roller obtained in the above steps at a tempering temperature of 600° C. for 6 hours;
[0032] (7) Finally, the tempered surfacing body is slowly cooled to 150°C with the furnace and then a...
PUM
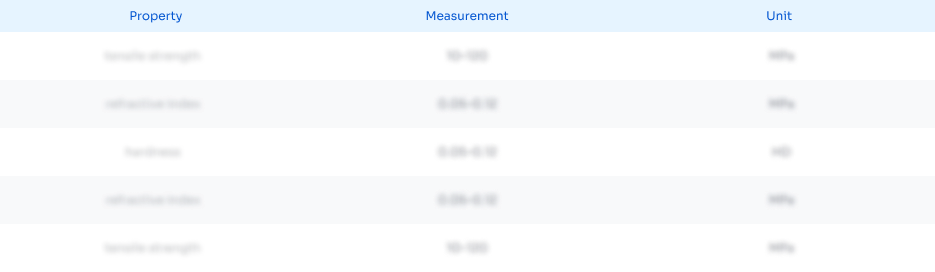
Abstract
Description
Claims
Application Information

- R&D
- Intellectual Property
- Life Sciences
- Materials
- Tech Scout
- Unparalleled Data Quality
- Higher Quality Content
- 60% Fewer Hallucinations
Browse by: Latest US Patents, China's latest patents, Technical Efficacy Thesaurus, Application Domain, Technology Topic, Popular Technical Reports.
© 2025 PatSnap. All rights reserved.Legal|Privacy policy|Modern Slavery Act Transparency Statement|Sitemap|About US| Contact US: help@patsnap.com