Method for industrialized production of N-alkyl substituted phosphoric triamide
A phosphoric triamide and alkylamine technology, applied in chemical instruments and methods, phosphate fertilizers, agriculture, etc., can solve the problems of difficult product separation and harsh production process requirements, achieve a simple product refining process, reduce operational difficulties, The effect of high product purity
- Summary
- Abstract
- Description
- Claims
- Application Information
AI Technical Summary
Problems solved by technology
Method used
Image
Examples
Embodiment 1
[0020] The production process in the No. 1 reactor:
[0021] Add 50Kg of PSCl in No. 1 reactor 3 , 384Kg CH 2 Cl 2 , stirred and cooled to 10°C, added dropwise 43.3Kg of n-butylamine, and controlled the rate of addition to keep the temperature of the reaction system at 10-12°C. After the dropwise addition was completed, the reaction system was heated under normal pressure and heated to reflux state, refluxed for 1 hour, cooled, added 50L of water to stir and extract, left to stand, the aqueous phase and the organic phase were separated, and the organic phase was dried by anhydrous sodium sulfate and then entered into 2 Standby in the No. reaction kettle.
[0022] The production process in the No. 2 reactor:
[0023] Under normal pressure, the reaction feed liquid in the No. 2 reactor was stirred and cooled to 10°C, 20.5Kg of ammonia gas was continuously introduced, the temperature of the reaction system was kept at 15-20°C, the stirring speed was 20rpm, and a large amount ...
Embodiment 2
[0031] The production process in the No. 1 reactor:
[0032] Add 50Kg of PSCl in No. 1 reactor 3 , 384Kg CH 2 Cl 2 , stirred and cooled to 10°C, added dropwise 62.7Kg of n-hexylamine, and controlled the rate of addition to keep the temperature of the reaction system at 10-12°C. After the dropwise addition is completed, the reaction system is heated under normal pressure and heated to reflux state, reflux reaction for 2 hours, cooled, added 50L of water to stir and extract, let stand, the water phase and the organic phase are separated, and the organic phase is dried by anhydrous calcium chloride and then enters Standby in No. 2 reactor.
[0033] The production process in the No. 2 reactor:
[0034] Under normal pressure, the reaction feed liquid in the No. 2 reactor was stirred and cooled to 10°C, 20.5Kg of ammonia gas was continuously introduced, the stirring speed was at 30rpm, the temperature of the reaction system was kept at 15-20°C, and a large amount of White NH 4...
Embodiment 3
[0042] The production process in the No. 1 reactor:
[0043] Add 50Kg of PSCl in No. 1 reactor 3 , 384Kg CH 2 Cl 2 , stirred and cooled to 10°C, added dropwise 45.3Kg of n-butylamine, and controlled the rate of addition to keep the temperature of the reaction system at 10-12°C. After the dropwise addition is completed, the reaction system is heated under normal pressure to reflux state, reflux reaction for 1 hour, cooled, add 50L of water to stir and extract, let stand, the water phase and the organic phase are separated, and the organic phase is dried by calcium oxide and enters the No. 2 reaction Reserve in the kettle.
[0044] The production process in the No. 2 reactor:
[0045] Under normal pressure, the reaction feed liquid in the No. 2 reactor was stirred and cooled to 10°C, 20.5Kg of ammonia gas was continuously introduced, the stirring speed was at 40rpm, the temperature of the reaction system was kept at 15-20°C, and a large amount of White NH 4 Cl solid. Ammo...
PUM
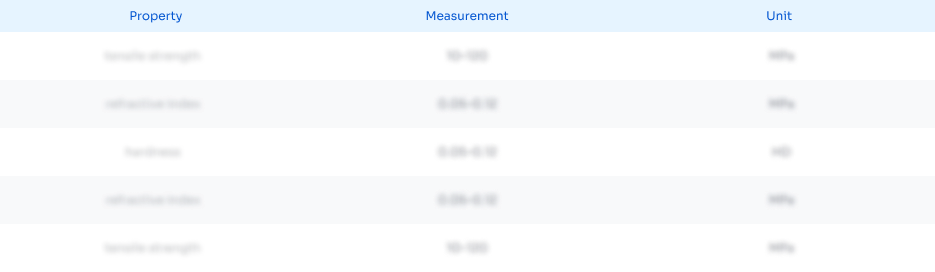
Abstract
Description
Claims
Application Information

- Generate Ideas
- Intellectual Property
- Life Sciences
- Materials
- Tech Scout
- Unparalleled Data Quality
- Higher Quality Content
- 60% Fewer Hallucinations
Browse by: Latest US Patents, China's latest patents, Technical Efficacy Thesaurus, Application Domain, Technology Topic, Popular Technical Reports.
© 2025 PatSnap. All rights reserved.Legal|Privacy policy|Modern Slavery Act Transparency Statement|Sitemap|About US| Contact US: help@patsnap.com