Vitrification reagent for preparing glass melt piece for X fluorescence analysis and use method thereof
A technology for fluorescence analysis and glass fusion, applied in the field of X-ray fluorescence analysis, can solve the problems of unstable analysis results, glass fusion rupture, long analysis period, etc., to achieve good fluidity, reduce fusion costs, and accurate and stable analysis results. Effect
- Summary
- Abstract
- Description
- Claims
- Application Information
AI Technical Summary
Problems solved by technology
Method used
Examples
Embodiment 1
[0026] Add anhydrous lithium tetraborate and boric acid into a three-dimensional mixer and mix to form the vitrification reagent of the present invention. The amount of boric acid added can be more or less. After a large number of experiments, it is best to mix 0.3-0.4 grams of boric acid in every eight grams of anhydrous lithium tetraborate. good. Mix the vitrification agent of the present invention with the metallurgical flux, put it into a platinum yellow pot and melt it at high temperature for 12-15 minutes, and make a glass frit after cooling.
Embodiment 2
[0028] In the mixture of anhydrous lithium tetraborate and lithium metaborate, add boric acid and mix with metallurgical flux. The amount of boric acid added can be more or less, and it is the best to mix 0.3-0.4 gram of boric acid in every eight grams of anhydrous lithium tetraborate and lithium metaborate mixture. Put the above sample into a platinum yellow pot and melt it at high temperature for 12-15 minutes, and make a glass frit after cooling.
Embodiment 3
[0030] Add anhydrous lithium tetraborate and boric acid into a three-dimensional mixer and mix to form the vitrification reagent of the present invention. The amount of boric acid added can be more or less. After a large number of experiments, it is best to mix 0.3-0.4 grams of boric acid in every eight grams of anhydrous lithium tetraborate. good. Mix the vitrification reagent of the present invention with iron-containing ore, put it into a platinum yellow pot and melt it at high temperature for 12-15 minutes, and make a glass frit after cooling.
PUM
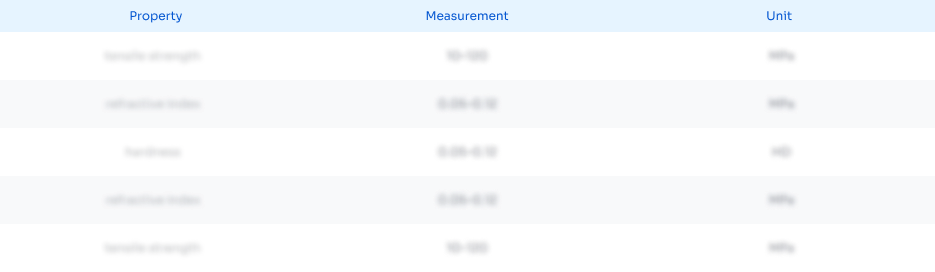
Abstract
Description
Claims
Application Information

- Generate Ideas
- Intellectual Property
- Life Sciences
- Materials
- Tech Scout
- Unparalleled Data Quality
- Higher Quality Content
- 60% Fewer Hallucinations
Browse by: Latest US Patents, China's latest patents, Technical Efficacy Thesaurus, Application Domain, Technology Topic, Popular Technical Reports.
© 2025 PatSnap. All rights reserved.Legal|Privacy policy|Modern Slavery Act Transparency Statement|Sitemap|About US| Contact US: help@patsnap.com