Flexible glue for coating ABS material and method for producing the same
A technology of ABS material and soft glue, which is applied in the field of soft glue covering ABS material and its preparation, which can solve the problems of insufficient material strength and hand feeling, easy whitening of the surface, and resistance to scratches, etc., to achieve ideal coating effect, Good scratch resistance, good flexibility effect
- Summary
- Abstract
- Description
- Claims
- Application Information
AI Technical Summary
Problems solved by technology
Method used
Examples
Embodiment 1
[0028] Weigh the SEBS with a weight ratio of 20% (the following are the weight ratios) and pour it into the blender. Slowly add 5% white oil to the SEBS, and slowly stir while adding it until the drop is completed. Stir evenly, and then press the TPU 55%, ABS 15%, compatibilizer 4%, 1010 / 168 0.2 / 0.1%, EBS 0.4%, E525 0.3%, weighed, poured into a blender and stirred evenly. The mixed material is put into the hopper of the twin-screw extruder, melted and blended, extruded and granulated to form a composite material. Among them, the temperature settings of each heating zone of the screw are: zone 1 temperature: 185°C; zone 2: 190°C; zone 3: 190°C; zone 4: 190°C; head: 185°C; residence time 1-2min. The pressure is 14MPa.
Embodiment 2
[0030] Weigh the SEBS with a weight ratio of 20% (the following are the weight ratios) and pour it into the blender. Slowly add 10% white oil to the SEBS, and slowly stir while adding it until the drop is completed. Stir evenly, and then press the TPU 50%, ABS 15%, compatibilizer 4%, 1010 / 168 0.2 / 0.1%, EBS 0.4%, E525 0.3%, weighed, poured into a blender and stirred evenly. The mixed material is put into the hopper of the twin-screw extruder, melted and blended, extruded and granulated to form a composite material. Among them, the temperature settings of each heating zone of the screw are: zone 1 temperature: 185°C; zone 2: 190°C; zone 3: 190°C; zone 4: 190°C; head: 185°C; residence time 1-2min. The pressure is 14MPa.
Embodiment 3
[0032]Weigh the SEBS with a weight ratio of 20% (the following are the weight ratios) and pour it into the blender. Slowly add 15% white oil to the SEBS, and slowly stir while adding it until the drop is completed. Stir evenly, and then press the TPU 45%, ABS 15%, compatibilizer 4%, 1010 / 168 0.2 / 0.1%, EBS 0.4%, E525 0.3%, weighed, poured into a blender and stirred evenly. The mixed material is put into the hopper of the twin-screw extruder, melted and blended, extruded and granulated to form a composite material. Among them, the temperature settings of each heating zone of the screw are: zone 1 temperature: 185°C; zone 2: 190°C; zone 3: 190°C; zone 4: 190°C; head: 185°C; residence time 1-2min. The pressure is 14MPa.
PUM
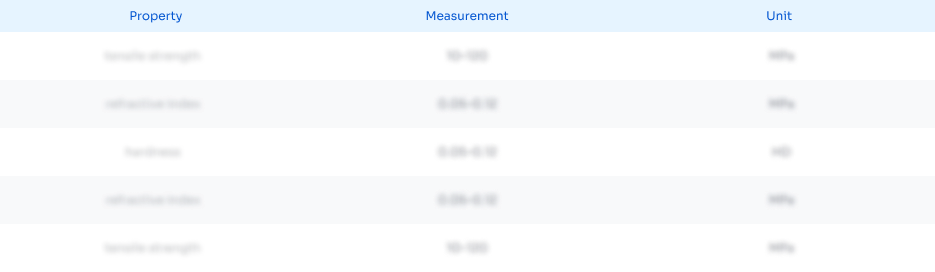
Abstract
Description
Claims
Application Information

- Generate Ideas
- Intellectual Property
- Life Sciences
- Materials
- Tech Scout
- Unparalleled Data Quality
- Higher Quality Content
- 60% Fewer Hallucinations
Browse by: Latest US Patents, China's latest patents, Technical Efficacy Thesaurus, Application Domain, Technology Topic, Popular Technical Reports.
© 2025 PatSnap. All rights reserved.Legal|Privacy policy|Modern Slavery Act Transparency Statement|Sitemap|About US| Contact US: help@patsnap.com