Preparation of vinyl aromatic polyether grafting concrete superplasticiser
A vinyl aromatic and superplasticizer technology, applied in the field of concrete superplasticizer, can solve the problems of environmental protection and lack of economy, and achieve the effects of low price, stable product performance and good slump retention
- Summary
- Abstract
- Description
- Claims
- Application Information
AI Technical Summary
Problems solved by technology
Method used
Examples
Embodiment 1
[0031] Under nitrogen protection, add 60.00 g of polyethylene glycol monomethyl ether with a molecular weight of 600, 10.00 g of maleic anhydride, and 0.05 g of 2,6-di-tert-butyl-p-cresol into the reactor, stir and heat, and raise the temperature to 60 At ℃, 1.80 g of sulfuric acid was added. Continue to heat up to 80°C, and react at this temperature for 2 hours to obtain an esterified product. In the reactor containing the esterification product, add 10.00 g of styrene, 0.50 g of vinyl acetate, and 0.40 g of dibenzoyl peroxide as an initiator. After reacting at 80°C for 4 hours, a copolymerized product was obtained.
[0032] Add 0.20 g of dehydrating agent phosphorus pentoxide to the copolymerized product, and stir for 15 minutes to disperse the dehydrating agent evenly. At 80°C, 10.00 g of concentrated sulfuric acid was added dropwise. After two hours of reaction, the temperature was raised to 120° C., and 40.00 g of acetyl sulfate was added. After continuing to react fo...
Embodiment 2
[0034] Under nitrogen protection, 120.00 g of polypropylene glycol monoethyl ether with a molecular weight of 1200, 60.00 g of maleic anhydride, and 0.30 g of p-phenylenediamine were added to the reactor, stirred and heated, and when the temperature was raised to 60°C, 6.00 g of sulfuric acid was added. Continue to heat up to 90°C, and react at this temperature for 2 hours to obtain an esterified product. In the reactor containing the esterification product, add 60.00 g of 9-vinylanthracene, 2.0 g of vinyl acetate, and 5.40 g of dibenzoyl peroxide as an initiator. After reacting at 90° C. for 3 h, a copolymerized product was obtained.
[0035] Add 1.20 g of dehydrating agent phosphorus pentoxide to the copolymerized product, and stir for 15 minutes to disperse the dehydrating agent evenly. At 80°C, 60.0 g of chlorosulfonic acid was added dropwise. After reacting for two hours, the temperature was raised to 160° C., and 120.00 g of lauroyl sulfate was added. After continuing...
Embodiment 3
[0037]Under the protection of nitrogen, add 100.00 g of polyethylene glycol monoethyl ether with a molecular weight of 1000, 20.00 g of maleic anhydride, and 0.20 g of 2,6-di-tert-butyl-p-cresol. Into the reactor, stir and heat, and raise the temperature to 60 At ℃, 4.00 g of phosphoric acid was added. Continue to heat up to 80°C, and react at this temperature for 3 hours to obtain an esterified product. In the reactor containing the esterification product, add 40.00 g of α-methylstyrene, 4.00 g of vinyl acetate, and 2.40 g of initiator tert-butyl peroxybenzoate. After reacting at 80° C. for 2 h, a copolymerized product was obtained.
[0038] Add 0.80 g of boric anhydride as a dehydrating agent to the copolymerized product, and stir for 15 minutes to disperse the dehydrating agent evenly. At 80°C, 40.00 g of sulfur trioxide was added dropwise. After two hours of reaction, the temperature was raised to 130° C., and 80.00 g of hexanoyl sulfate was added. After continuing the...
PUM
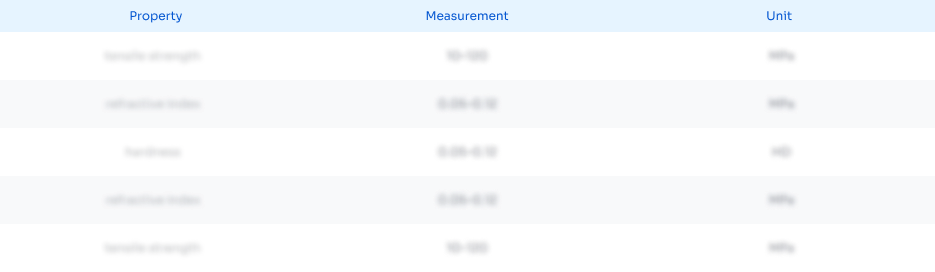
Abstract
Description
Claims
Application Information

- Generate Ideas
- Intellectual Property
- Life Sciences
- Materials
- Tech Scout
- Unparalleled Data Quality
- Higher Quality Content
- 60% Fewer Hallucinations
Browse by: Latest US Patents, China's latest patents, Technical Efficacy Thesaurus, Application Domain, Technology Topic, Popular Technical Reports.
© 2025 PatSnap. All rights reserved.Legal|Privacy policy|Modern Slavery Act Transparency Statement|Sitemap|About US| Contact US: help@patsnap.com