Vapor-liquid separation method of segmented vapor-liquid phase change heat exchanger
A technology of phase change heat exchanger and vapor-liquid separation, applied in the direction of heat exchanger shell, indirect heat exchanger, heat exchanger type, etc., can solve the limitation of condensate flow range, insufficient suction force, large-scale production and installation Work difficulties and other problems, achieve the effect of ingenious structural design and ensure the ability of steam resistance
- Summary
- Abstract
- Description
- Claims
- Application Information
AI Technical Summary
Problems solved by technology
Method used
Image
Examples
Embodiment 1
[0036] like Figure 6 , Figure 7 As shown, the liquid leakage and steam arresting device 10 of the present invention includes a base plate 11 having the same cross-sectional size as the heat exchanger header 2. The center of the base plate 11 has a main hole 12 with an equivalent diameter of 2 to 5 mm and the same aperture, surrounding the main hole 12 is evenly arranged with a circle of auxiliary holes 13 with an equivalent diameter less than 2mm and the same equivalent aperture. When the condensed liquid generated in the heat exchange tube 1 upstream of the heat exchanger 2 is less, the liquid separated from the header 2 will form a layer of liquid film on the surface of the main hole 12 and the auxiliary hole 13 of the substrate 11, preventing liquid and vapor The solid flows out from the main hole 12 and the auxiliary hole 13; when the liquid volume increases slightly, the main hole 12 with a larger aperture will seep first, which is equivalent to the drainage of a singl...
Embodiment 2
[0038] like Figure 8 , Figure 9 As shown, the size range of the main hole 12 and the auxiliary hole 13 in the present embodiment is similar to that of Embodiment 1, the difference is that the main hole 12 and the auxiliary hole 13 are frustum holes with variable equivalent apertures, and the equivalent apertures can be larger at the top and lower at the bottom. Small; it can also be small at the top and large at the bottom, and it can also be in any form of variable cross-sectional area. This structure can make both the main hole 12 and the auxiliary hole 13 able to carry a certain amount of condensate, and when the amount of condensate in the main hole is relatively low, it can also ensure the continuous drainage and prevent steam from passing through; the auxiliary hole 13 Condensate in the pores can improve its steam resistance ability and prevent steam from passing through. It can also improve the steam resistance ability and accelerate liquid discharge according to the...
Embodiment 3
[0040] like Figure 10 , Figure 11 As shown, the main hole 12 and the auxiliary hole 13 in this embodiment intersect with each other, presenting a "plum blossom" hole structure. The intersecting plum-blossom hole structure can be regarded as an extended structure of the main hole. Compared with the single main hole 12 structure, its flow equivalent diameter is increased, which can effectively strengthen the condensate flow capacity of the main hole 12, while the auxiliary hole 13 Intersecting with the main hole 12 can adhere a certain amount of condensate through surface tension when the amount of liquid is relatively small, which strengthens the vapor resistance and liquid sealing ability of the device.
PUM
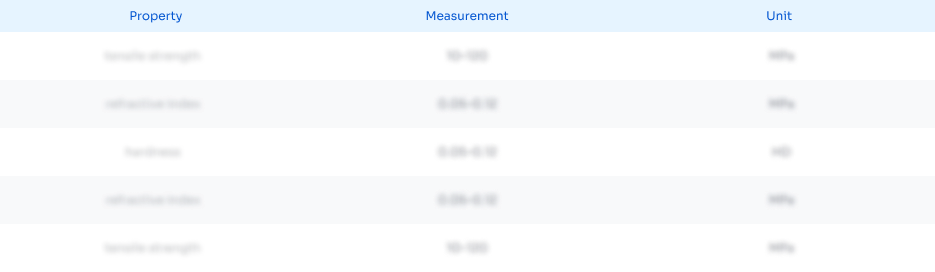
Abstract
Description
Claims
Application Information

- R&D
- Intellectual Property
- Life Sciences
- Materials
- Tech Scout
- Unparalleled Data Quality
- Higher Quality Content
- 60% Fewer Hallucinations
Browse by: Latest US Patents, China's latest patents, Technical Efficacy Thesaurus, Application Domain, Technology Topic, Popular Technical Reports.
© 2025 PatSnap. All rights reserved.Legal|Privacy policy|Modern Slavery Act Transparency Statement|Sitemap|About US| Contact US: help@patsnap.com