Computer-aided design method for cam curve of three-component zooming system
A computer-aided, cam curve technology, applied in computing, special data processing applications, instruments, etc., can solve problems such as affecting the processing process of cams and cam curves, complicated calculations, and poor fusion system performance, etc. Excellent quality, good craftsmanship, and the effect of improving imaging quality
- Summary
- Abstract
- Description
- Claims
- Application Information
AI Technical Summary
Problems solved by technology
Method used
Image
Examples
Embodiment 1
[0023] It is an embodiment of designing the cam curve of a three-component zoom lens for projection. The design method is: install ZEMAX optical design software on the computer used in the auxiliary design, and adjust the cam curve track according to the three-component optical system Based on the requirements of Gaussian optics and the macro language function of ZEMAX, compile the 3-CAM-ZPL program on the ZEMAX optical design software platform, run the program, and the program will automatically analyze the distribution of each zoom group of the three-component system, input Sampling points, calculate the transition parameters of the optical system, input the bending coefficient K of the second zoom group U2, calculate the zoom cam curve data by the 3-CAM.ZPL program, run the 3-CAM.ZPL program, and the program automatically judges each zoom group Whether interlacing occurs during the moving process, and a prompt message is output. If such a situation occurs, it means that the ...
Embodiment 2
[0027] see Figure 4 , the steps of the design method are the same as in Embodiment 1. In this embodiment, the second zoom group U2 is selected to move in a curve (curved toward the object side), that is, K>0, and the number of sampling points is set to 10, and the 3-CAM.ZPL program is run to calculate The result is as follows:
[0028] K=0.03 Ave-MTF=0.6995 Max-AveMTF=0.7113 Min-AveMTF=0.6752
[0029] From the calculation data of Example 2, it can be seen that when K=0.03 of the second zoom group U2, that is, when the curve is slightly bent toward the object side, the value of Ave-MTF changes from 0.6842 when moving in a straight line to 0.6995, and the performance of the zoom system has seen an increase.
Embodiment 3
[0031] see Figure 5 , the steps of the design method are the same as in Embodiment 1. In this embodiment, the second zoom group U2 is selected to move in a curve (curved to the image plane), that is, K<0, the number of sampling points is set to 10, and the 3-CAM.ZPL program is run to calculate The result is as follows:
[0032] K=-0.05: Ave-MTF=0.6483 Max-AveMTF=0.7047 Min-AveMTF=0.6017
[0033] From the calculation data of Example 3, it can be seen that when K of the second zoom group U2=-0.05, that is, when the curve is slightly bent toward the image side, the value of Ave-MTF changes from 0.6842 when moving straight to 0.6483, and the zoom system Performance has been reduced.
[0034] from image 3 , Figure 4 , Figure 5 It can be seen that when the curvature coefficient K of the second zoom group U2 is different, the bending direction and degree of the curve of the third zoom group U3 are also different. When K=0, it means linear movement, K>0 means the curve bends t...
PUM
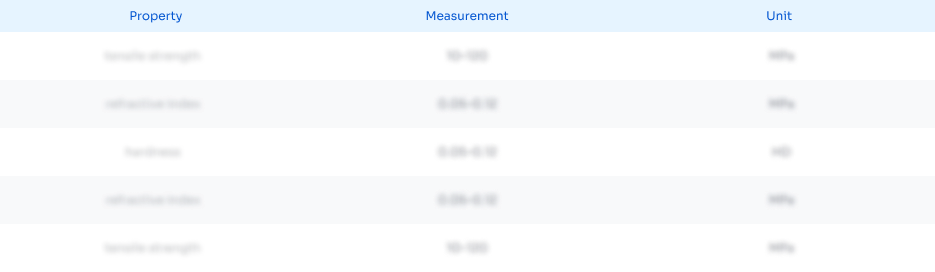
Abstract
Description
Claims
Application Information

- R&D
- Intellectual Property
- Life Sciences
- Materials
- Tech Scout
- Unparalleled Data Quality
- Higher Quality Content
- 60% Fewer Hallucinations
Browse by: Latest US Patents, China's latest patents, Technical Efficacy Thesaurus, Application Domain, Technology Topic, Popular Technical Reports.
© 2025 PatSnap. All rights reserved.Legal|Privacy policy|Modern Slavery Act Transparency Statement|Sitemap|About US| Contact US: help@patsnap.com