Method for producing biodegradable plastic from activated sludge
A technology for biodegrading plastics and activated sludge, applied in the field of environmental biology, can solve problems such as insufficient mass concentration, and achieve the effects of no need for sterile conditions, easy operation, and saving initial investment.
- Summary
- Abstract
- Description
- Claims
- Application Information
AI Technical Summary
Problems solved by technology
Method used
Image
Examples
Embodiment 1
[0022] The inventive method adopts technological process to see figure 1 . The activated sludge with polyhydroxyalkanoate storage capacity was cultivated by dynamic substrate dosing. First, 1 liter of activated sludge from a sewage treatment plant was inoculated in the sequencing batch reactor 3 (effective volume 2 liters), and then air was charged through the air pump 4 to start the aerobic reaction, which lasted 6 hours in total. In the first 10 minutes of the aerobic reaction, the mineral salt culture solution containing volatile fatty acids in the culture solution storage tank 1 is injected into the sequencing batch reactor 3 at a constant speed by the peristaltic pump 2, and the injection amount of the culture solution is 1 liter, and mixed The sludge concentration in the liquid is controlled at MLSS=2500~5000mg / L, and the concentration of the culture liquid is controlled at about 120Cmmol / L. 5 minutes before the end of the aerobic reaction, 83 ml of the mixture was dis...
Embodiment 2
[0026] The technological process of embodiment 2 is identical with embodiment 1, but concrete operation parameter is different, and difference is:
[0027] 1) The dosing time of the culture medium is increased from 10 minutes to 30 minutes;
[0028] 2) The aerobic reaction time of sequence batch reactor 3 is increased to 12 hours by 6 hours;
[0029] 3) The aerobic reaction time of reactor 5 is increased to 12 hours by 10 hours;
[0030] 4) The components and concentrations of the culture solution are different. The components of the culture solution used in Example 2 and the concentration of each component are: every liter of deionized water contains 30 cmmol of acetic acid, propionic acid, butyric acid and valeric acid, and 480 mg of ammonium sulfate, 200 mg of magnesium chloride, and 30 mg of valeric acid. EDTA, 240mg dipotassium hydrogen phosphate, 60mg potassium dihydrogen phosphate, 100mg calcium chloride, 40mg yeast extract and 2mL trace element solution. Trace elemen...
Embodiment 3
[0033] The technological process of embodiment 3 is identical with embodiment 1, but concrete operation parameter is different, and difference is:
[0034] 1) The dosing time of the culture medium is increased from 10 minutes to 20 minutes;
[0035] 2) The aerobic reaction time of sequence batch reactor 3 is reduced to 4 hours by 6 hours;
[0036]3) The aerobic reaction time of reactor 5 is reduced to 2 hours by 10 hours;
[0037] The culture solution used in embodiment 3 is the same as that in embodiment 1, but the sludge concentration in the mixed solution is controlled at MLSS=2500~5000mg / L, and the concentration of the culture solution is controlled at 60Cmmol / L. In embodiment 3, the productive rate of polyhydroxyalkanoate is 0.57Cmmol / Cmmol, polyhydroxyalkanoate weight accounts for 42% of microbial cell dry weight in microbial cell
PUM
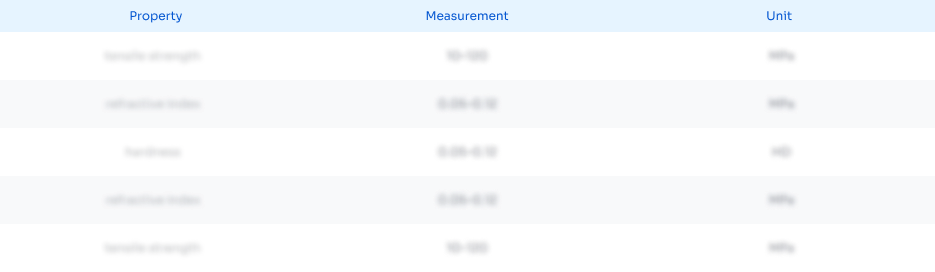
Abstract
Description
Claims
Application Information

- R&D
- Intellectual Property
- Life Sciences
- Materials
- Tech Scout
- Unparalleled Data Quality
- Higher Quality Content
- 60% Fewer Hallucinations
Browse by: Latest US Patents, China's latest patents, Technical Efficacy Thesaurus, Application Domain, Technology Topic, Popular Technical Reports.
© 2025 PatSnap. All rights reserved.Legal|Privacy policy|Modern Slavery Act Transparency Statement|Sitemap|About US| Contact US: help@patsnap.com