Titanium and titanium alloy consumable electrode noble gas protective welding technique
An inert gas and shielded welding technology, applied in welding medium, welding equipment, welding equipment, etc., can solve the problems of slow welding speed, large residual stress, welding deformation, etc., reduce unit energy input, improve overall quality, and improve welding production The effect of improving efficiency
- Summary
- Abstract
- Description
- Claims
- Application Information
AI Technical Summary
Problems solved by technology
Method used
Image
Examples
Embodiment 1
[0029] Using the invented molten inert gas shielded welding technology, the welding of TC4 titanium alloy deep sea test frame with plate thickness of 8mm+10mm and structure size of 3300mm × 3600mm × 4200mm is carried out. The welding process adopts the push-pull wire feeding method and adopts the TC3 grade. The welding wire, the droplet transfer form is jet transfer, the welding arc is a combination of pulsed and continuous combustion arcs, and the welding of two positions of fixed flat welding and horizontal welding is completed; the welding joints are designed as "T" joint fillet welds and Butt welds in the form of corner joints.
[0030] The blunt edge thickness h of the groove ranges from 0mm to 4mm, the assembly clearance p ranges from 0 to 5mm, and the groove angles α and β range from 40° to 70°. For joint and bevel forms see image 3 and Figure 4 shown.
[0031] When manually controlling the welding torch to realize the welding operation, the moving speed of the wel...
Embodiment 2
[0038] Using the invented molten electrode inert gas shielded welding technology, a double-layer, hyperboloid TA5 titanium alloy diversion structure simulation body with a plate thickness of 4mm+16mm, a length of 1200mm, a width of 750mm and a height of 400mm was welded. The welding process adopts The push-pull wire feeding method adopts TA4 grade welding wire, the droplet transfer form is a combination of short-circuit and jet transfer, and the welding arc is a combination of pulsed and continuous combustion arcs to achieve fixed flat welding, vertical welding and horizontal welding. welding; welded joints are designed as backing butt welds and “T” joint fillet welds.
[0039] The blunt edge thickness h of the groove ranges from 0mm to 4mm, the assembly clearance p ranges from 0 to 5mm, and the groove angles α and β range from 40° to 70°. For joint and bevel forms see figure 1 and image 3 shown.
[0040] When manually controlling the welding torch to realize the welding o...
Embodiment 3
[0047] Using the invented molten electrode inert gas shielded welding technology, the welding process of the double-layer, hyperboloid TA5+TA2 titanium alloy diversion structure entity with the traveling structure size of 2000mm × 2200mm × 3300mm adopts the push-pull wire feeding method. For the welding wires of TA4 and TA2 grades, the droplet transfer form is jet transfer, and the welding arc is a combination of pulsed and continuous combustion arcs, to complete the four positions of fixed flat welding, vertical welding, horizontal welding and overhead welding; welding joints include Butt welds with and without backing plates, "T" joint fillet welds, and butt welds in the form of fillet joints.
[0048] The blunt edge thickness h of the groove ranges from 0mm to 4mm, the assembly clearance p ranges from 0 to 5mm, and the groove angles α and β range from 40° to 70°. For joint and bevel forms see figure 1 , figure 2 , image 3 and Figure 4 shown.
[0049] When manually c...
PUM
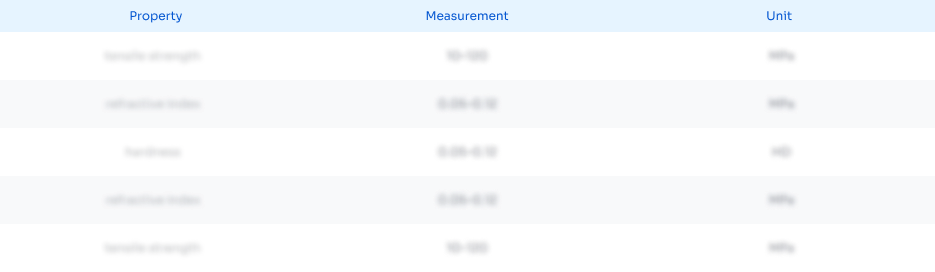
Abstract
Description
Claims
Application Information

- R&D Engineer
- R&D Manager
- IP Professional
- Industry Leading Data Capabilities
- Powerful AI technology
- Patent DNA Extraction
Browse by: Latest US Patents, China's latest patents, Technical Efficacy Thesaurus, Application Domain, Technology Topic, Popular Technical Reports.
© 2024 PatSnap. All rights reserved.Legal|Privacy policy|Modern Slavery Act Transparency Statement|Sitemap|About US| Contact US: help@patsnap.com