Fixation joint part dynamics parameter identification method for machine tool
A technology of dynamic parameters and identification methods, applied in scientific instruments, mechanical devices, instruments, etc., can solve the problems of lack of universality, neglect of coupling characteristics, and lack of consideration of tangential mechanical characteristics of joints, etc. Identify the effects of high accuracy and rich dynamics
- Summary
- Abstract
- Description
- Claims
- Application Information
AI Technical Summary
Problems solved by technology
Method used
Image
Examples
Embodiment Construction
[0031] Concrete implementation steps of the present invention are as follows:
[0032] 1) Investigate the various forms of fixed joints of common machine tools, give the division criteria of the finite element model of the fixed joint, extract its essential properties, and establish a "parametric" joint dynamics model;
[0033] 2) Perform finite element analysis on the substructure and extract the substructure mass matrix M 0 and the stiffness matrix K 0 , the substructure is generally made of steel, and the material damping of this material itself is very small. In this case, 90% of the internal damping of the machine tool structure comes from the joint of the machine tool, so the damping matrix of the substructure C 0 Combined with the damping matrix C 1 negligible compared to
[0034] 3) According to the node correspondence of the "parameterized" joint element dynamic model, using the finite element matrix assembly theory, the substructure stiffness matrix K 0 and the ...
PUM
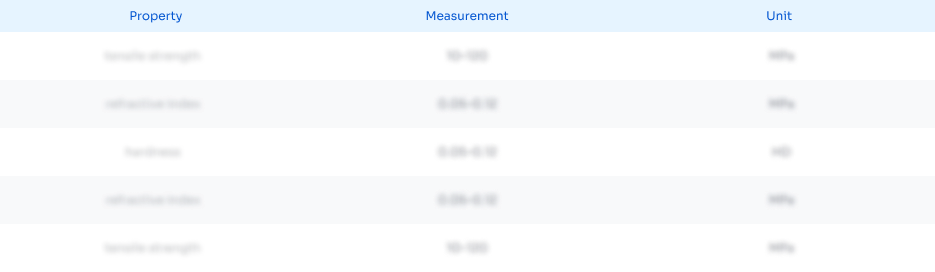
Abstract
Description
Claims
Application Information

- R&D Engineer
- R&D Manager
- IP Professional
- Industry Leading Data Capabilities
- Powerful AI technology
- Patent DNA Extraction
Browse by: Latest US Patents, China's latest patents, Technical Efficacy Thesaurus, Application Domain, Technology Topic, Popular Technical Reports.
© 2024 PatSnap. All rights reserved.Legal|Privacy policy|Modern Slavery Act Transparency Statement|Sitemap|About US| Contact US: help@patsnap.com