Method for improving RH vacuum furnace bottom groove life
A technology of bottom tank and vacuum furnace, which is applied in the field of RH vacuum refining equipment, can solve the problems of low service life and frequent maintenance of the bottom tank of RH vacuum furnace, and achieve the effect of increasing service life, increasing average service life and obvious effect
- Summary
- Abstract
- Description
- Claims
- Application Information
AI Technical Summary
Problems solved by technology
Method used
Image
Examples
Embodiment Construction
[0009] The present invention will be further described below through embodiments with reference to the accompanying drawings.
[0010] Firstly, an argon blowing system 6 is added on the opposite side of the argon blowing system 5 on one side of the vacuum chamber 4 of the RH vacuum furnace, that is, on the side of the downcomer 1 of the dip tube. When the dipping tube has reached the end of its service life and the vacuum chamber 4 needs to be off-line for maintenance, remove the dipping tube ascending pipe 2 and descending pipe 1, and after knotting the circulating pipe 3, install the descending pipe 1 at the position of the original ascending pipe 2 , Install the rising pipe 2 at the position of the original descending pipe 1, and exchange the positions of the two. Then connect the argon gas in the riser 2 to the newly added argon blowing system 6, and after the replacement, it can continue to be used. Adopting this method can effectively improve the service life of the bot...
PUM
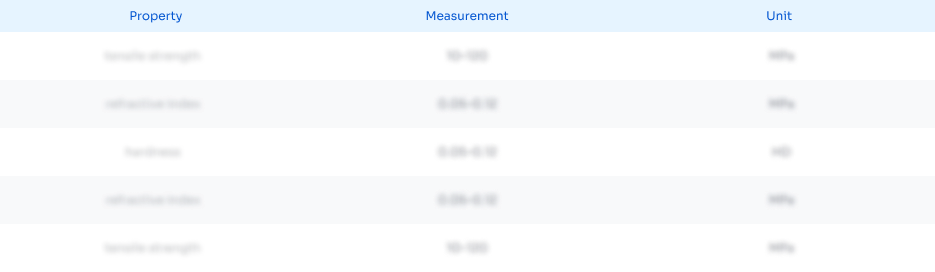
Abstract
Description
Claims
Application Information

- Generate Ideas
- Intellectual Property
- Life Sciences
- Materials
- Tech Scout
- Unparalleled Data Quality
- Higher Quality Content
- 60% Fewer Hallucinations
Browse by: Latest US Patents, China's latest patents, Technical Efficacy Thesaurus, Application Domain, Technology Topic, Popular Technical Reports.
© 2025 PatSnap. All rights reserved.Legal|Privacy policy|Modern Slavery Act Transparency Statement|Sitemap|About US| Contact US: help@patsnap.com