Novel industrial waste gypsum self forming energy-saving process
A self-curing technology of industrial waste gypsum, which is applied in the field of building materials, can solve the problems of affecting cement performance, incomplete modification, and large investment in treatment, and achieve the effects of improving quality, saving drying energy consumption, and less investment
- Summary
- Abstract
- Description
- Claims
- Application Information
AI Technical Summary
Problems solved by technology
Method used
Image
Examples
Embodiment 1
[0022] Phosphogypsum in a certain place is a gray water-containing bulk material, with a natural moisture content of 18.7%, and a soluble phosphate and fluorophosphate content of 2.74%. Curing agent, mixed by weight phosphogypsum: modified curing agent=70:30 ratio, formed into Φ10mm gypsum rod with a roller extrusion molding machine, self-curing drying time 2 days, cement plant comparative test, gypsum rod using comprehensive The performance is better than natural gypsum, the strength is 1.71MPa higher than 3d, and 2.3MPa 28d higher, and the setting time is equivalent to natural gypsum.
Embodiment 2
[0024] The desulfurization gypsum of a power plant is a light yellow bulk material with a water content of 13.4%. The modified curing agent is compounded with methyl cellulose, potassium sulfate and lime, and the ratio of desulfurized gypsum:modified curing agent=99:1 is mixed , extruded into a Φ8mm material rod, and the natural curing and drying time is 3 days. It is used in the comparison test between the cement plant and the natural gypsum. The setting time is the same. The strength increases by 1.83MPa in 3 days, and the strength increases by 3.1MPa in 28 days.
Embodiment 3
[0026] Waste gypsum from a citric acid factory, gray-black, with a moisture content of 23.4%, and a peculiar smell, was compounded with lime, bentonite, slag powder, potassium permanganate, water reducing agent UF, triethanolamine, and potassium sulfate to form a modified and solidified product. agent, mixed according to the ratio of lemon gypsum: modified curing agent = 89:11, extruded into a Φ8mm material rod, self-cured and dried for 3 days, and the odor is completely eliminated. It is used in the comparison test of cement plant and natural gypsum. The setting time Only prolonging for 5 minutes, the strength increased by 3.31MPa in 3 days and 4.73MPa in 28 days.
PUM
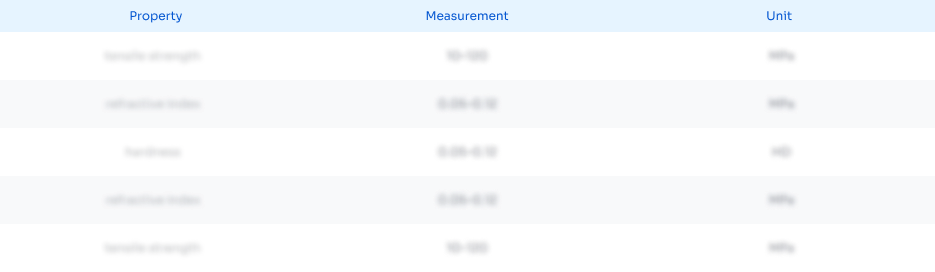
Abstract
Description
Claims
Application Information

- R&D Engineer
- R&D Manager
- IP Professional
- Industry Leading Data Capabilities
- Powerful AI technology
- Patent DNA Extraction
Browse by: Latest US Patents, China's latest patents, Technical Efficacy Thesaurus, Application Domain, Technology Topic, Popular Technical Reports.
© 2024 PatSnap. All rights reserved.Legal|Privacy policy|Modern Slavery Act Transparency Statement|Sitemap|About US| Contact US: help@patsnap.com