Superficial treatment process of high abrasion resistance metallic film synthetic leather
A surface treatment and metal film technology, applied in the field of metal film synthetic leather surface treatment technology, can solve the problems of affecting product quality, surface color fading, performance degradation, etc., to achieve the same color and transparency of the metal surface, and good surface wear resistance. , the effect of improving quality
- Summary
- Abstract
- Description
- Claims
- Application Information
AI Technical Summary
Problems solved by technology
Method used
Examples
Embodiment 1
[0032] The proportion of the colorless film mixed slurry by weight is:
[0033] KT254W thermoplastic polyurethane TPU resin 100
[0034] Anti-sticking agent amino-modified polysiloxane of grade T257 0.5
[0035] Dimethylformamide DMF 30
[0036] The viscosity of the prepared mixed slurry is 1800cps / 25℃
[0037] The coating thickness of the colorless film mixed slurry is 15 filaments, and the mixed slurry forms a transparent protective film with a thickness of 5 filaments on the surface of the metal film. The wear resistance is good, but the cost is relatively high. Product wear resistance test results: H18 grinding head 225 revolutions, Martindale grinding 11000 times, the same metal film synthetic leather has not been surface treated by the method of the present invention, and its wear resistance: H18 grinding head 35 revolutions, Martindale Grind 2600 times.
Embodiment 2
[0039] The proportion of the colorless film mixed slurry by weight is:
[0040] KT254W thermoplastic polyurethane TPU resin 100
[0041] Anti-sticking agent amino-modified polysiloxane of grade T257 0.5
[0042] Dimethylformamide DMF 38
[0043] The viscosity of the prepared mixed slurry is 1500cps / 25℃
[0044] The coating thickness of the colorless film mixed slurry is 14 filaments. The mixed slurry can form a protective film with a thickness of 4 filaments on the surface of the metal film, with good wear resistance and moderate cost. Product wear resistance test results: H18 grinding head 180 revolutions, Martindale grinding 90000 times, the same metal film synthetic leather has not been surface treated by the method of the present invention, and its wear resistance: H18 grinding head 35 revolutions, Martindale Grind 2600 times.
Embodiment 3
[0046] The proportion of the colorless film mixed slurry by weight is:
[0047] KT254W thermoplastic polyurethane TPU resin 100
[0048] Anti-sticking agent amino-modified polysiloxane of grade T257 0.5
[0049] Dimethylformamide DMF 45
[0050] The viscosity of the prepared mixed slurry is 1200cps / 25℃
[0051] The coating thickness of the colorless film mixed slurry is 13 filaments. The mixed slurry can form a protective film with a thickness of 2 filaments on the surface of the metal film. The wear resistance is slightly worse than the ratio 1 and the ratio 2, and the cost is low. Product wear resistance test results: H18 grinding head 120 revolutions, Martindale grinding 50,000 times, the same metal film synthetic leather has not been surface treated by the method of the present invention, and its wear resistance: H18 grinding head 35 revolutions, Martindale Grind 2600 times.
PUM
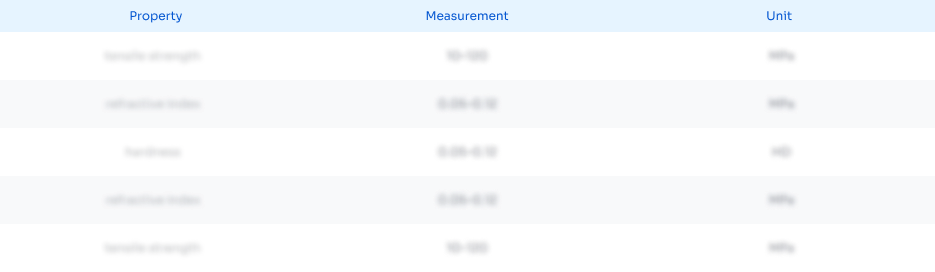
Abstract
Description
Claims
Application Information

- R&D
- Intellectual Property
- Life Sciences
- Materials
- Tech Scout
- Unparalleled Data Quality
- Higher Quality Content
- 60% Fewer Hallucinations
Browse by: Latest US Patents, China's latest patents, Technical Efficacy Thesaurus, Application Domain, Technology Topic, Popular Technical Reports.
© 2025 PatSnap. All rights reserved.Legal|Privacy policy|Modern Slavery Act Transparency Statement|Sitemap|About US| Contact US: help@patsnap.com