Gas phase SO3 film-scrapping sulfonating technology
A technology of scraping film and gas phase, which is applied in the field of gas phase SO3 scraping film sulfonation process, can solve the problems of inappropriate sulfonation of heat-sensitive materials, unguaranteed product conversion rate, and high difficulty of circulating spraying, so as to overcome easy atomization and prolong The effect of sulfonation time and small investment
- Summary
- Abstract
- Description
- Claims
- Application Information
AI Technical Summary
Problems solved by technology
Method used
Image
Examples
Embodiment 2
[0030] Embodiment 2, the sulfonation of fatty alcohol ether: liquid SO 3 It enters the evaporator by metering, after vaporization, it is cooled by the cooler, the temperature is 42-45°C, it enters from the bottom of the sulfonation reactor, and is mixed with the dilution gas in the sulfonation reactor in the stirring shaft to form a reaction gas (control the gas volume concentration) : 3%), the reaction gas enters the reaction cylinder through the reaction gas distribution hole on the top of the stirring shaft from bottom to top at a speed of 20m / s, and flows downward with the fatty alcohol polyoxyethylene ether (3) (average molar mass 340 ) for full contact reaction, control the sulfonation temperature: 33~35℃, liquid SO 3 / fatty alcohol polyoxyethylene ether (3) molar ratio: 1.01:1; after the sulfonated product is discharged from the outlet of the reaction product, it is neutralized with triethanolamine to obtain triethanolamine sulfate of fatty alcohol ether.
Embodiment 3
[0031] Embodiment 3, toluene sulfonation: liquid SO 3 It enters the evaporator by metering, after being vaporized, it is cooled by a cooler at a temperature of 35-38°C, and enters from the bottom of the sulfonation reactor, and the reaction gas is mixed with the dilution gas in the sulfonation reactor in the stirring shaft (to control the gas volume concentration) : 5.0%), the reaction gas enters the reaction cylinder from bottom to top through the reaction gas distribution hole on the upper part of the stirring shaft at a speed of 10m / s, and contacts and reacts with toluene flowing downward, and the sulfonation temperature is controlled: 13~15℃ , liquid SO 3 / toluene molar ratio: 1:1; after the sulfonated product is discharged from the outlet of the reaction product, it is aged to obtain the toluenesulfonic acid product.
Embodiment 4
[0032] Example 4, Preparation of Petroleum Sulfonate by Sulfonation of Petroleum Diesel Wax: Liquid SO 3 It enters the evaporator by metering, after vaporization, it is cooled by a cooler, the temperature is 60-62°C, it enters from the bottom of the sulfonation reactor, and is mixed with the dilution gas in the sulfonation reactor in the stirring shaft to form a reaction gas (control the gas volume concentration) : 3.5%), the reaction gas enters the reaction cylinder from bottom to top through the reaction gas distribution hole on the upper part of the stirring shaft at a speed of 6m / s, and fully contacts and reacts with the downstream petroleum diesel wax. The sulfonation temperature: 65 ~68°C, control the neutralization value of the sulfonated product: 80~100KOHmg / kg; after the sulfonated product is discharged from the outlet of the reaction product, it is neutralized with 25% ammonia water to obtain petroleum ammonium sulfonate.
PUM
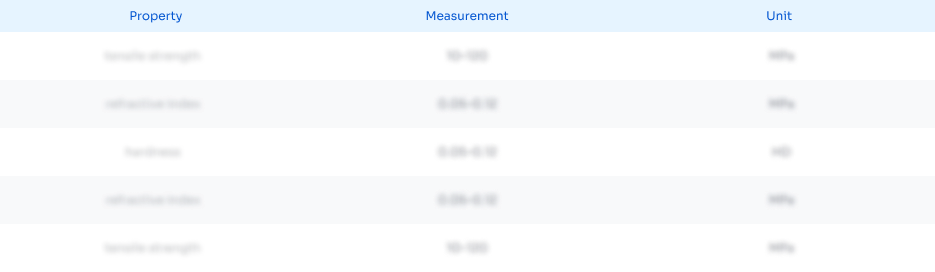
Abstract
Description
Claims
Application Information

- R&D
- Intellectual Property
- Life Sciences
- Materials
- Tech Scout
- Unparalleled Data Quality
- Higher Quality Content
- 60% Fewer Hallucinations
Browse by: Latest US Patents, China's latest patents, Technical Efficacy Thesaurus, Application Domain, Technology Topic, Popular Technical Reports.
© 2025 PatSnap. All rights reserved.Legal|Privacy policy|Modern Slavery Act Transparency Statement|Sitemap|About US| Contact US: help@patsnap.com