Casting powder for casting magnesium aluminum alloy
A technology of mold slag and magnesium alloy, applied in the field of metal casting, can solve the problems of aggravated magnesium combustion, poor thermal conductivity, and oxide wrinkle, and achieve the effect of enhancing the feeding effect, reducing the tendency of thermal cracking, and free of oxide wrinkle.
- Summary
- Abstract
- Description
- Claims
- Application Information
AI Technical Summary
Problems solved by technology
Method used
Examples
Embodiment 1
[0013] Embodiment 1: A magnesium alloy foundry mold flux, its composition weight percent is: artificial mica suspending agent 69%; alkylsulfonate sodium flame retardant 31%.
[0014] A total amount of 6% of a binder can also be added to the above-mentioned mold powder, and the binder can be selected from silica sol or aluminum phosphate.
Embodiment 2
[0015] Embodiment 2: A magnesium alloy casting mold flux, its composition weight percent is: 55% of bentonite suspending agent; 45% of boric acid flame retardant.
[0016] A binder of 5% in total can also be added to the mold flux, and the binder can be silica sol or aluminum phosphate.
Embodiment 3
[0017] Embodiment 3: A magnesium alloy casting mold flux, the mold flux components in weight percent are: diatomite, suspending agent 6%; boric acid flame retardant 40%.
[0018] A total amount of 5-6% of a binder can also be added to the mold flux, and the binder can be silica sol or aluminum phosphate.
PUM
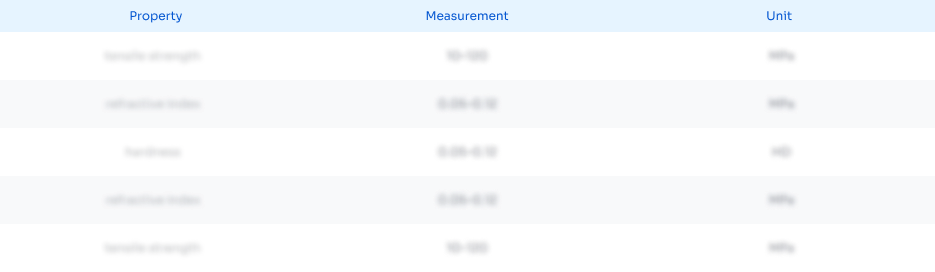
Abstract
Description
Claims
Application Information

- R&D
- Intellectual Property
- Life Sciences
- Materials
- Tech Scout
- Unparalleled Data Quality
- Higher Quality Content
- 60% Fewer Hallucinations
Browse by: Latest US Patents, China's latest patents, Technical Efficacy Thesaurus, Application Domain, Technology Topic, Popular Technical Reports.
© 2025 PatSnap. All rights reserved.Legal|Privacy policy|Modern Slavery Act Transparency Statement|Sitemap|About US| Contact US: help@patsnap.com