Sandwiched thermal-insulating wall and its production
A technology for thermal insulation walls and manufacturing methods, applied to walls, building components, coverings/linings, etc., can solve problems such as thermal insulation, poor thermal insulation performance, high cost, and long construction period, and achieve strong thermal insulation performance and long service life long life, less environmental pollution
- Summary
- Abstract
- Description
- Claims
- Application Information
AI Technical Summary
Problems solved by technology
Method used
Image
Examples
Embodiment Construction
[0030] The manufacturing method of the sandwich thermal insulation wall of the present invention will be described in detail below in conjunction with the embodiments.
[0031] The manufacturing method of the sandwich insulation wall of the present invention is completed by the following steps:
[0032] The first step is to assemble the decorative grille 7 and make the outer eaves decorative layer 1 .
[0033] Such as figure 1 As shown, first select the decorative material of the desired outer eaves decorative pattern, assemble the decorative grille 7 according to the size of the outer eaves decorative material and the designed wall size; then inlay the selected decorative materials 9 into the decorative grille one by one 7, and make the back of the decorative material 9 on the top, and ensure that the thickness of the decorative material 9 is greater than the thickness of the frame of the decorative grille, so that the decorative material 9 is higher than the frame of the de...
PUM
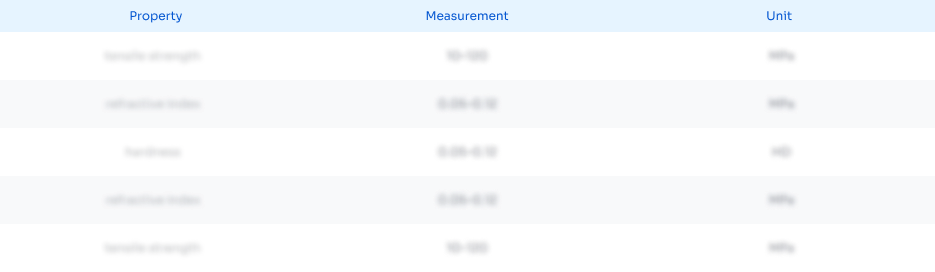
Abstract
Description
Claims
Application Information

- Generate Ideas
- Intellectual Property
- Life Sciences
- Materials
- Tech Scout
- Unparalleled Data Quality
- Higher Quality Content
- 60% Fewer Hallucinations
Browse by: Latest US Patents, China's latest patents, Technical Efficacy Thesaurus, Application Domain, Technology Topic, Popular Technical Reports.
© 2025 PatSnap. All rights reserved.Legal|Privacy policy|Modern Slavery Act Transparency Statement|Sitemap|About US| Contact US: help@patsnap.com