Method for recycling high purity molybdenum from molybdenum-containing spent catalyst
A technology of waste catalyst and soda ash, applied in the direction of improving process efficiency, can solve the problems of difficult to completely remove, pollute the environment, low recovery rate of molybdenum, etc., and achieve the effect of low cost, low risk and improved purity
- Summary
- Abstract
- Description
- Claims
- Application Information
AI Technical Summary
Problems solved by technology
Method used
Examples
Embodiment 1
[0031] 10.0g contains 16w% MoO 3 Industrial MoO 3 / Alumina waste catalyst, after being pulverized to 120 mesh, fully mixed with 10g of soda ash and 5g of magnesium oxide, kept at 70°C for 2 hours, and adjusted the oxygen content to 5.0v%; at 240°C for 2 hours, adjusted the oxygen content Gradually increase to 12.0v%, keep the temperature at 430°C for 2 hours, gradually increase the oxygen content to 18.0v%; keep the temperature at 530°C for 2 hours, gradually increase the oxygen content to 21v%. The heating rate was 5°C per minute. After cooling, soak in water at 80°C for 2h, filter and wash the precipitate fully, and separate. The pH of the filtrate was adjusted to 8.5 with concentrated sulfuric acid, and then filtered; the pH of the filtrate was adjusted to 1.2 with nitric acid to precipitate molybdenum acid, and then separated by filtration. Add molybdic acid to ammonia water to dissolve, then adjust the pH value to 3.0 with nitric acid to precipitate ammonium molybdate,...
Embodiment 2
[0033] 10.0g contains 20w% MoO 3 Industrial MoO 3 / alumina-silica waste catalyst, crushed to 120 mesh, fully mixed with 15g of sodium potassium carbonate and 5g of magnesium oxide, kept at 70°C for 2 hours, and adjusted the oxygen content to 5.0v%; kept at 240°C for 2 hours Hours, gradually increase the oxygen content to 12.0v%, keep the temperature at 430°C for 2 hours, gradually increase the oxygen content to 18.0v%; keep the temperature at 540°C for 2 hours, gradually increase the oxygen content to 21v%, The heating rate between each section is 8°C per minute. After cooling, soak in water at 70°C for 3 hours, filter and fully wash the precipitate, and separate. The filtrate was first adjusted to pH 8.5 with concentrated sulfuric acid, and then filtered; MgSO with a liquid-solid ratio (weight ratio) of 10:1 was added to the filtrate 4 , Stir for 1h, filter; then adjust the pH of the filtrate to 1.2 with nitric acid to precipitate molybdic acid, and separate by filtration. ...
Embodiment 3
[0035] 10.0g contains 24w% MoO 3 Industrial MoO 3 / alumina-silicon oxide waste catalyst, after pulverizing to 150 mesh, directly mixes fully with sodium hydroxide and magnesium oxide (sodium hydroxide 5g, magnesium oxide is 5g). Keep the temperature at 70°C for 1 hour, adjust the oxygen content to 5.0v%,; keep the temperature at 250°C for 2 hours, gradually increase the oxygen content to 12.0v%, and keep the temperature at 450°C for 2 hours, gradually increase the oxygen content It is 18.0v%; keep the temperature at 550°C for 3 hours, gradually increase the oxygen content to 21v%, and the temperature rise rate between each stage is 5°C per minute. After cooling, add 40mL of water for leaching, and stir at 90°C for 3h. Filter and wash the precipitate well and separate. The filtrate was first adjusted to pH 9.0 with concentrated sulfuric acid, and filtered; the liquid-solid ratio (weight ratio) was added to the filtrate with Mg(NO 3 ) 2 , Stir for 1h, filter; then adjust th...
PUM
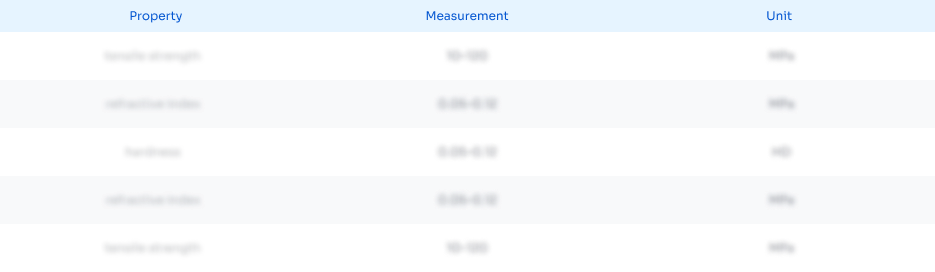
Abstract
Description
Claims
Application Information

- R&D
- Intellectual Property
- Life Sciences
- Materials
- Tech Scout
- Unparalleled Data Quality
- Higher Quality Content
- 60% Fewer Hallucinations
Browse by: Latest US Patents, China's latest patents, Technical Efficacy Thesaurus, Application Domain, Technology Topic, Popular Technical Reports.
© 2025 PatSnap. All rights reserved.Legal|Privacy policy|Modern Slavery Act Transparency Statement|Sitemap|About US| Contact US: help@patsnap.com