Process for preparing SCR denitration catalyst and SCR denitration catalyst prepared by the method
A denitrification catalyst, a certain amount of technology, applied in molecular sieve catalysts, chemical instruments and methods, physical/chemical process catalysts, etc., can solve the problem that the catalyst does not have resistance to sulfur dioxide oxidation
- Summary
- Abstract
- Description
- Claims
- Application Information
AI Technical Summary
Problems solved by technology
Method used
Examples
Embodiment 1
[0020] Dissolve 10 grams of ferrous ammonium sulfate in 100 grams of water, add 50 grams of nano TiO under stirring 2 After stirring evenly, add 50 grams of A-type molecular sieve, stir until dry under heating, and dry at 100° C. for 5 hours. Then at 200°C, calcine with oxygen for 1 hour, and then calcined at 400°C for 10 hours under nitrogen to obtain the required catalyst. The denitrification efficiency is 91%, the sulfur dioxide oxidation rate is <1%, and the denitrification rate remains at the original 99% after 300 hours. %, sulfur dioxide oxidation rate <1%.
Embodiment 2
[0022] Dissolve 10 grams of ferrous ammonium sulfate in 100 grams of water, add 50 grams of nano TiO under stirring 2 , and then add 50 grams of X-type molecular sieves, stir until dry under heating, and dry at 100° C. for 5 hours. Then at 300°C, calcine with oxygen for 2 hours, and then calcined at 450°C for 5 hours under nitrogen to obtain the required catalyst. The denitrification efficiency is 92%, the sulfur dioxide oxidation rate is <1%, and the denitrification rate remains at the original 98% after 300 hours. %, sulfur dioxide oxidation rate <1%.
Embodiment 3
[0024] Dissolve 8 grams of ferrous ammonium sulfate in 100 grams of water, add 70 grams of nano TiO under stirring 2 , and then add 30 grams of X-type molecular sieves, stir until dry under heating, and dry at 100° C. for 5 hours. Then at 350°C, calcine with oxygen for 3 hours, and then calcined at 350°C for 5 hours under nitrogen to obtain the required catalyst. The denitrification efficiency is 90%, the sulfur dioxide oxidation rate is <1%, and the denitrification rate remains at the original 96% after 300 hours. %, sulfur dioxide oxidation rate <1%.
PUM
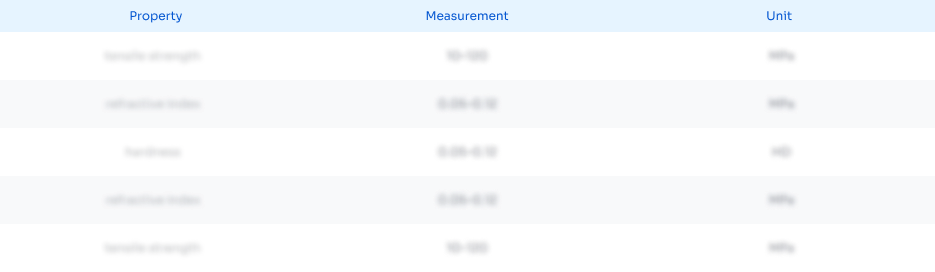
Abstract
Description
Claims
Application Information

- R&D Engineer
- R&D Manager
- IP Professional
- Industry Leading Data Capabilities
- Powerful AI technology
- Patent DNA Extraction
Browse by: Latest US Patents, China's latest patents, Technical Efficacy Thesaurus, Application Domain, Technology Topic, Popular Technical Reports.
© 2024 PatSnap. All rights reserved.Legal|Privacy policy|Modern Slavery Act Transparency Statement|Sitemap|About US| Contact US: help@patsnap.com