Bobtail tension rivet and riveting method
A technology of pulling rivets and short tails, applied to rivets and other directions, can solve the problems of complex structure and system of rotary riveters, long riveting time of pulling rivets, large riveting space, etc., and achieve fast riveting speed, reduced riveting steps, and good installation Effect
- Summary
- Abstract
- Description
- Claims
- Application Information
AI Technical Summary
Problems solved by technology
Method used
Image
Examples
Embodiment 1
[0039] Example 1: See Figure 1- Figure 6 ,
[0040]See Fig. 1, the short-tail pull rivet of 'ring groove riveting', nail shank 2A has polished rod section 2.1, ring groove section 2.2A and short thin ring groove section 2.3. Generally, due to processing requirements, there is a processing transition section between the polished rod section 2.1 and the ring groove section 2.2A; a step needs to be processed between the ring groove section 2.2A and the short thin ring groove section 2.3. The length L of the short thin ring groove segment 2.3 2.3 The value range is 11.1-14.8mm, corresponding to the marked diameter D 2.3 The value range is 11.6-20.0mm, usually the length L of the short thin ring groove segment is 2.3 2.3 and diameter D 2.3 The selection is designed according to the tension of the riveter 6, the structure and size of the chuck 6.1.
[0041] See Figure 2- image 3 , the inner hole of the collar 3A is a light hole, and the size of the collar 3A matches the rin...
Embodiment 2
[0048] Example 2: See Figure 7- Figure 12 'Thread riveted' stub rivets.
[0049] As shown in Fig. 7, the structure of the nail rod 2B in embodiment 2 is different from that in Fig. 1 in embodiment 1 as follows: the threaded segment 2.2B is used to replace the ring groove segment 2.2A. The remaining nail heads, polished rod section 2.1 and short thin ring groove section 2.3 are all the same.
[0050] See Figure 8 , The structure of the collar 3B in Embodiment 2 is different from that in Figure 2 of Embodiment 1 as follows: a threaded segment 3B3 is provided at the rear port of the inner hole of the collar 3B. The front end of the collar 3B has the same disc 3B1 as in Embodiment 1 and a detection point 3B2 on the rear end of the disc.
[0051] For the riveting steps of 'thread riveting' short tail rivets, see Figure 9 , Figure 10, Figure 11 and Figure 12 , where Figure 10, Figure 11 and Figure 12 The second step, the riveting step (ii) and the riveting step (iii) of t...
PUM
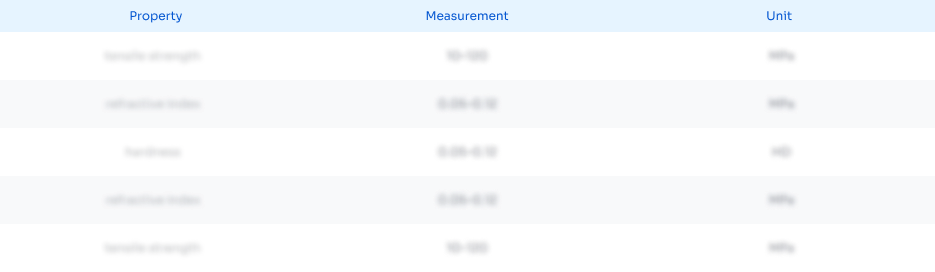
Abstract
Description
Claims
Application Information

- Generate Ideas
- Intellectual Property
- Life Sciences
- Materials
- Tech Scout
- Unparalleled Data Quality
- Higher Quality Content
- 60% Fewer Hallucinations
Browse by: Latest US Patents, China's latest patents, Technical Efficacy Thesaurus, Application Domain, Technology Topic, Popular Technical Reports.
© 2025 PatSnap. All rights reserved.Legal|Privacy policy|Modern Slavery Act Transparency Statement|Sitemap|About US| Contact US: help@patsnap.com