Method for producing dichlorohydrin with glycerol
A technology of dichloropropanol and glycerin, which is applied in the introduction of halogen preparation, organic chemistry, etc., can solve the problems affecting the reaction rate and equipment utilization rate, achieve the improvement of reaction rate and HCl utilization rate, simplify the reaction process, increase the rate and HCl The effect of utilization
- Summary
- Abstract
- Description
- Claims
- Application Information
AI Technical Summary
Problems solved by technology
Method used
Image
Examples
Embodiment 1
[0028] Such as figure 1 As shown, the mixture of glycerol (99% by mass industrial product) and acetic acid (wherein the acetic acid catalyst accounts for 4% of the total mass of glycerol) is first mixed uniformly in the mixer 1, and then the above-mentioned mixture is fed at a rate of 1mol / h The pump 9 feeds the material into the tank reactor 2, HCl gas is passed into the tank reactor 2 at 1.5 mol / h, and the reaction residence time of the above-mentioned materials in the tank reactor 2 is 3 h. Sampling by the sampling valve 18 for gas chromatographic analysis shows that the conversion rate of glycerin is 88.2%, the generation rate of monochloropropanediol is 79.3%, and the generation rate of dichloropropanol is 6.8%.
[0029]The reaction liquid from the tank reactor 2 is pumped to the preheater 13 through the discharge pump 10, heated to a specified temperature of 80° C. through the preheater 13, and then pumped through the pump (not shown in the figure) to the reactive rectif...
Embodiment 2
[0035] The mixture of glycerin (99% by mass) and acetic acid is first mixed uniformly in the mixer 1, and then fed to the tank reactor 2 through the feed pump 9 at 1mol / h, and HCl gas is fed into the tank reactor at 1.5mol / h. Reactor 2, the reaction residence time is 5h. Samples are taken through sampling valve 18 for gas chromatographic analysis. It can be seen that the conversion rate of glycerin is 93.2%, the production rate of monochloropropanediol is 87.3%, and the production rate of dichloropropanol is 7.9%. All the other operations are the same as in Example 1.
[0036] Within 3 hours of steady-state operation, 3 mol of glycerol and 7.5 mol of HCl were fed, and glycerol was almost completely converted. The condensate collected from the top of reactive distillation column 3 was 111.2 g, and the amount collected from the top of purification distillation column 4 was 342.7 g. Dichloropropanol yield is 82.1% (shown in Table 1).
Embodiment 3
[0038] The mixture of glycerol (99% by mass) and adipic acid (wherein the adipic acid catalyst accounts for 4% of the total mass of glycerol) is first mixed uniformly in mixer 1, and then fed to 1.5 mol / h through feed pump 9 to In the tank reactor 2, HCl gas is passed into the tank reactor 2 at 1.5mol / h, and the reaction residence time is 3h. Samples are taken through sampling valve 18 for gas chromatographic analysis. It can be seen that the conversion rate of glycerin is 92.4%, the production rate of monochloropropanediol is 82.7%, and the production rate of dichloropropanol is 7.4%. All the other operations are the same as in Example 1.
[0039] The condensate collected from the top of reactive distillation column 3 was 257.4 g, and the amount collected from the top of purification distillation column 4 was 506.1 g. Dichloropropanol yield is 89.9% (shown in Table 1).
PUM
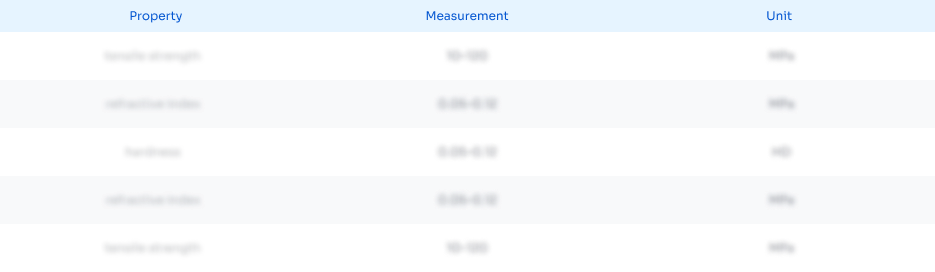
Abstract
Description
Claims
Application Information

- Generate Ideas
- Intellectual Property
- Life Sciences
- Materials
- Tech Scout
- Unparalleled Data Quality
- Higher Quality Content
- 60% Fewer Hallucinations
Browse by: Latest US Patents, China's latest patents, Technical Efficacy Thesaurus, Application Domain, Technology Topic, Popular Technical Reports.
© 2025 PatSnap. All rights reserved.Legal|Privacy policy|Modern Slavery Act Transparency Statement|Sitemap|About US| Contact US: help@patsnap.com