Method for producing xylon molded body and xylon molded body
A manufacturing method and a technology for a formed body, which are applied in the directions of manufacturing tools, wood compression, humidity-conditioning wood, etc., to achieve the effects of short processing time, low thermal conductivity, and shortened time.
- Summary
- Abstract
- Description
- Claims
- Application Information
AI Technical Summary
Problems solved by technology
Method used
Image
Examples
Embodiment 1
[0109] First, sawdust produced when sawing Japanese cedar at a wood processing factory is prepared as a raw material—wood powder for wooden materials. Adjust the moisture content of the woody material to 12%. Subsequently, after retorting at 215° C. for 6 minutes, drying was performed so that the water content of the wood flour was 8%. Subsequently, the wood flour was filled into a forming mold with a diameter of 140 mm, and compression-molded at room temperature under a pressure of 20 MPa for 30 seconds to obtain a preform. The preform was again placed in a φ140mm forming mold, and compression-molded under the condition of 30MPa for 2 minutes. The surface of the wood molded body obtained through the above process was free from stains due to gas generation, and was a glossy molded body. The 24-hour immersion water absorption rate is also below 1%, and there is no smell of organic acid.
Embodiment 2
[0111] Shavings of hinoki wood are prepared as a wood material as a raw material for moldings. Adjust the moisture content of the woody material to 12%. Subsequently, after retorting at 215° C. for 6 minutes, it was filled into a φ140 mm molding die, and compression-molded at room temperature under a pressure of 30 MPa for 3 minutes to obtain a preform. The preform was again placed in a forming mold with a diameter of 140 mm, and compression-molded at 200° C. and 30 MPa for 2 minutes. Also in this case, a molded article with a low water absorption rate and very little generation of organic acid can be obtained.
experiment example 1
[0115] In order to verify the effects of the present invention, the odors of the wood shaped articles obtained in Examples 1, 2 and Comparative Example 1 were measured. Specifically, the emitted amount of an organic acid which is a source of an odor was measured. Table 1 shows the emission amount μg / L of acetic acid and formic acid in each of the wooden shaped articles prepared in Examples 1, 2 and Comparative Example 1.
[0116] Table 1
[0117] Acetic acid (μg / L) Formic acid (μg / L) Example 1 <0.5
0.6 Example 2 <0.5
0.8 comparative example 9.2 10.2
[0118] As can be seen from Table 1, according to Examples 1 and 2 in which the moisture content of the wood material was adjusted to 8% and 12% respectively before the cooking process, and then molded, a wood molded body with little odor can be obtained due to the small amount of organic acid. Contrary to this time, in Comparative Example 1 in which drying was not performed before reto...
PUM
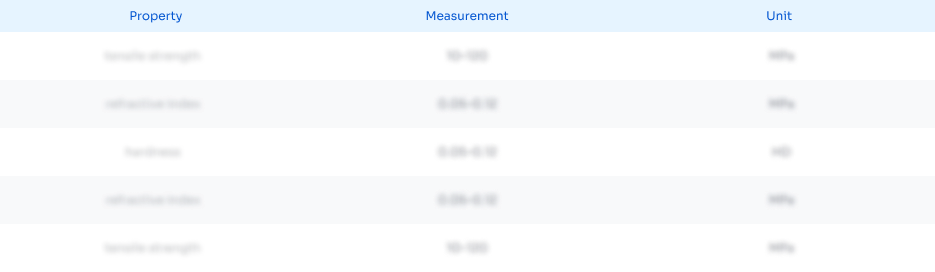
Abstract
Description
Claims
Application Information

- R&D
- Intellectual Property
- Life Sciences
- Materials
- Tech Scout
- Unparalleled Data Quality
- Higher Quality Content
- 60% Fewer Hallucinations
Browse by: Latest US Patents, China's latest patents, Technical Efficacy Thesaurus, Application Domain, Technology Topic, Popular Technical Reports.
© 2025 PatSnap. All rights reserved.Legal|Privacy policy|Modern Slavery Act Transparency Statement|Sitemap|About US| Contact US: help@patsnap.com