Method for preparing humic acid and salt thereof by oxidation and degradation of brown coal
A technology of oxidative degradation and humate, applied in the direction of organic chemistry, can solve the problems of difficult large-scale production, increased extraction rate, environmental pollution, etc., and achieve the effect of increasing yield, improving utilization rate, and simple production process
- Summary
- Abstract
- Description
- Claims
- Application Information
AI Technical Summary
Problems solved by technology
Method used
Image
Examples
Embodiment 1
[0035] Example 1: 100kg120 mesh lignite was added to the reactor, 0.10kg sucrose ester was added, and 250 liters of hydrogen peroxide with a mass fraction of 15% was added in 5 times at 30°C under stirring conditions, and fully stirred at a constant temperature until no large amount of hydrogen peroxide was produced. Until the foam is formed, let it react at room temperature for 12 hours. After the reaction was completed, it was centrifuged, the supernatant was filtered, and the filtrate was concentrated and dried to obtain 19.5 kg of water-soluble fulvic acid crude product. Add concentration of 0.25mol L to the precipitate obtained by centrifugation -1 2,000 liters of NaOH, reacted at 25°C for 20 hours, centrifuged after the reaction was completed, and the concentration of the supernatant was 1mol L -1 neutralized hydrochloric acid to a pH value of 1.5, centrifuged, precipitated and dried to obtain 35.02kg of brown humic acid.
Embodiment 2
[0036] Example 2: 100kg of 70-mesh lignite is added to the reactor, 0.12kg of sucrose ester is added, and 215 liters of hydrogen peroxide with a mass fraction of 17.5% is added in 5 times at 35°C under stirring conditions, and fully stirred at a constant temperature of 35°C until no longer It was allowed to react for 5 hours under the same conditions until a large amount of foam was generated. After the reaction was completed, it was centrifuged, the supernatant was suction filtered, and the filtrate was concentrated and dried to obtain 19.9 kg of crude water-soluble fulvic acid. Add concentration of 1.0mol L to the precipitate obtained by centrifugation -1 500 liters of NaOH, reacted at 25°C for 15 hours, centrifuged after the reaction was completed, and the concentration of the supernatant was 1mol L -1 The hydrochloric acid was neutralized to a pH value of 1.7, centrifuged, precipitated and dried to obtain 34.08kg of brown humic acid.
Embodiment 3
[0037] Example 3: 100kg of 80-mesh lignite was added to the reactor, 0.20kg of sucrose ester was added, and 200 liters of hydrogen peroxide with a mass fraction of 15% was added in 5 times at 40°C under stirring conditions, and fully stirred at a constant temperature of 40°C until no longer It was allowed to react for 40 minutes under the same conditions until foaming occurred. After the reaction was completed, it was centrifuged, the supernatant was filtered, and the filtrate was concentrated and dried to obtain 20.86 kg of crude water-soluble fulvic acid. The concentration of 0.25mol L was added to the residue precipitate after the production of fulvic acid -1 2000 liters of NaOH, reacted at 25°C for 15 hours, centrifuged after the completion of the reaction, and the concentration of the supernatant was 1mol L -1 The hydrochloric acid was neutralized to a pH value of 1.7, centrifuged, precipitated and dried to obtain 33.53kg of brown humic acid.
PUM
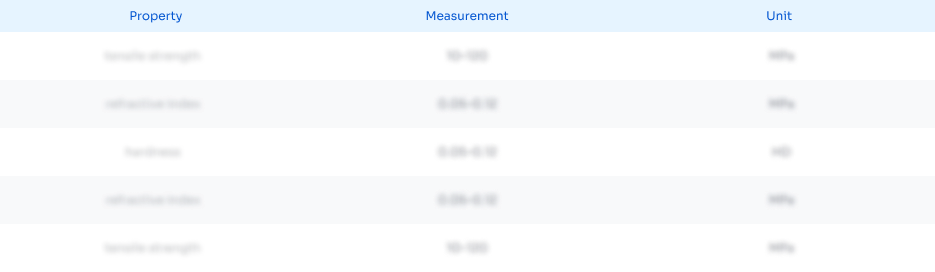
Abstract
Description
Claims
Application Information

- R&D
- Intellectual Property
- Life Sciences
- Materials
- Tech Scout
- Unparalleled Data Quality
- Higher Quality Content
- 60% Fewer Hallucinations
Browse by: Latest US Patents, China's latest patents, Technical Efficacy Thesaurus, Application Domain, Technology Topic, Popular Technical Reports.
© 2025 PatSnap. All rights reserved.Legal|Privacy policy|Modern Slavery Act Transparency Statement|Sitemap|About US| Contact US: help@patsnap.com