Reflow furnace
A reflow furnace and heater technology, which is used in electric heating devices, electrical components, printed circuit manufacturing, etc., can solve the problems of overheating, thermal damage to solder paste of electronic components, and inability to heat printed circuit boards, and achieves excellent thermal stability. The effect of increasing the heat capacity
- Summary
- Abstract
- Description
- Claims
- Application Information
AI Technical Summary
Problems solved by technology
Method used
Image
Examples
Embodiment Construction
[0053] Hereinafter, the reflow furnace of this invention is demonstrated based on drawing. Fig. 1 is the front sectional view of reflow oven of the present invention, figure 2 It is a front sectional view of the hot air blowing heater installed in the reflow furnace of the present invention, image 3 is a side sectional view of hot air blowing out of the heater, Figure 4 It is a perspective view of various heater units forming a component nozzle, and Fig. 5 is a top view of a zigzag-shaped hot air blown out of the heater by the component nozzle, Figure 6 It is a partially enlarged perspective view of FIG. 5, and FIG. 7 is a top view of a hot air blowing heater with a wave-shaped nozzle of the component, Figure 8 It is a partially enlarged perspective view of FIG. 7, and FIG. 9 is a top view of a hot air blowing heater whose component nozzle is a louver-shaped section.
[0054] As shown in FIG. 1 , the reflow furnace 1 of the present invention has a tunnel-shaped muffle f...
PUM
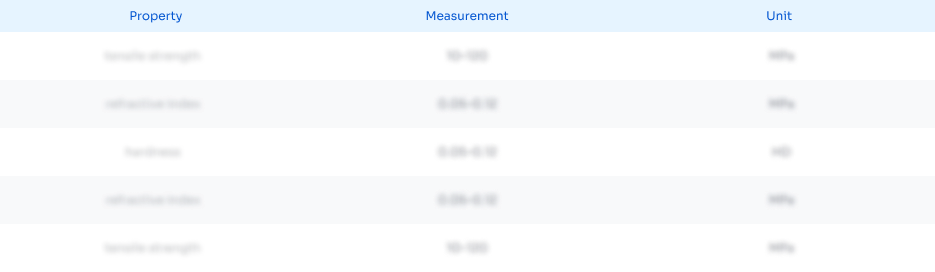
Abstract
Description
Claims
Application Information

- Generate Ideas
- Intellectual Property
- Life Sciences
- Materials
- Tech Scout
- Unparalleled Data Quality
- Higher Quality Content
- 60% Fewer Hallucinations
Browse by: Latest US Patents, China's latest patents, Technical Efficacy Thesaurus, Application Domain, Technology Topic, Popular Technical Reports.
© 2025 PatSnap. All rights reserved.Legal|Privacy policy|Modern Slavery Act Transparency Statement|Sitemap|About US| Contact US: help@patsnap.com