Enclosed type method and device for conveying zinc alloy liquor and casting zinc alloy ingot
A zinc alloy, closed technology, applied in the direction of feeding molten metal into the mold, casting equipment, metal processing equipment, etc., can solve the problems of high oxidation slag rate, high energy consumption, no molding, etc., and achieve high strength , good thermal insulation performance, and the effect of improving product quality
- Summary
- Abstract
- Description
- Claims
- Application Information
AI Technical Summary
Problems solved by technology
Method used
Image
Examples
Embodiment 1
[0030] The invention discloses a method for casting zinc alloy ingots by conveying zinc alloy liquid in a closed manner. After solid zinc is melted into a liquid and alloyed with alloying elements, the zinc alloy is pumped out by a pump and cast by a pipeline in a closed conveyance manner.
[0031] A device for airtight delivery of zinc alloy liquid casting zinc alloy ingots, as shown in Figure 1 to image 3 As shown, it includes melting equipment, extraction equipment, conveying equipment, and casting mold 5. The melting equipment is an alloy melting furnace 1, the extraction equipment is a zinc liquid pump 3, and the zinc liquid pump 3 is a submerged pump structure. The flow rate of the zinc liquid pump 3 is determined by Controlled by a frequency converter, the liquid zinc pump 3 is installed in the small melting pool 2 of a square closed steel container with a size of 1000mm×1000mm×1000mm connected to the inner cavity of the alloy melting furnace 1; the small melting pool 2...
Embodiment 2
[0033] The invention discloses a method for casting zinc alloy ingots by conveying zinc alloy liquid in a closed manner. After solid zinc is melted into a liquid and alloyed with alloying elements, the zinc alloy is extracted by a pump and cast in a closed conveyance manner through a pipeline.
[0034] A device for conveying zinc alloy liquid casting zinc alloy ingots in a closed manner, as shown in Figure 1, image 3 , Figure 4 As shown, it includes melting equipment, extraction equipment, conveying equipment, and casting equipment 5. The melting equipment is an alloy melting furnace 1, the extraction equipment is a zinc liquid pump 3, and the zinc liquid pump 3 is a submerged vertical centrifugal pump with a motor power of 2.2kw , the flow rate of the zinc liquid pump 3 is controlled by a frequency converter, and the zinc liquid pump 3 is installed in a small melting pool 2 with a specification of 1000mm×1000mm×1000mm connected to the inner cavity of the alloy smelting furn...
PUM
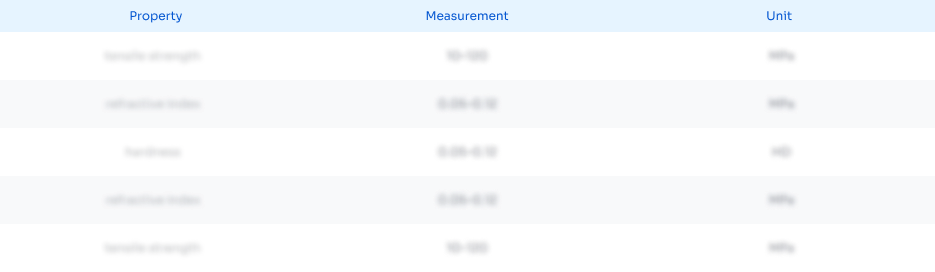
Abstract
Description
Claims
Application Information

- R&D Engineer
- R&D Manager
- IP Professional
- Industry Leading Data Capabilities
- Powerful AI technology
- Patent DNA Extraction
Browse by: Latest US Patents, China's latest patents, Technical Efficacy Thesaurus, Application Domain, Technology Topic, Popular Technical Reports.
© 2024 PatSnap. All rights reserved.Legal|Privacy policy|Modern Slavery Act Transparency Statement|Sitemap|About US| Contact US: help@patsnap.com