Fast dry and cold setting starch strengthened glue and preparation method thereof
A technology for strengthening glue and starch, which is applied in the direction of starch adhesive, adhesive type, reinforcing agent addition, etc. It can solve the problems of slow bonding speed, low bonding strength, poor water resistance, etc., and achieve fast bonding speed, Strong waterproof performance, simple production equipment and process
- Summary
- Abstract
- Description
- Claims
- Application Information
AI Technical Summary
Problems solved by technology
Method used
Examples
Embodiment 1
[0014] Materials and proportions: corn starch 460kg, potassium pyroantimonate 3kg, dehydrated alum 10kg, light magnesium oxide 10kg, borax 16kg, solid sodium hydroxide 6kg, aluminum sulfate 2kg, polyvinyl alcohol 10kg, baking soda 5kg, water 1205kg.
[0015] Preparation: (1) Prepare component A: put the dehydrated alum into a drying furnace, raise the temperature to 135° C., after drying, drop to normal temperature and discharge, crush and sieve, and mix evenly with light magnesium oxide; (2) Preparation of component B: add 60kg cornstarch to 100kg water to prepare starch slurry; add sodium hydroxide aqueous solution (dissolve sodium hydroxide in 25kg water) for gelation; then add aluminum sulfate and mix at 70°C for 30 minutes , and mixed with 250kg of cold water, and stirred evenly; (3) Preparation of component C: dissolve potassium pyroantimonate in another container with 30kg of water, then dilute with 800kg of water at 35°C, add borax and 400kg of cornstarch, and mix evenl...
Embodiment 2
[0018] Materials and proportioning: corn starch 575kg, potassium pyroantimonate 4kg, dehydrated alum 6kg, light magnesium oxide 7kg, borax 6kg, solid sodium hydroxide 10kg, aluminum sulfate 1kg, polyvinyl alcohol 5kg, baking soda 8kg, water 1320kg.
[0019] Preparation: (1) Prepare component A: put the dehydrated alum into a drying furnace, raise the temperature to 135° C., after drying, drop to normal temperature and discharge, crush and sieve, and mix evenly with light magnesium oxide; (2) Prepare component B: add 25kg cornstarch to 90kg water to prepare starch slurry; add sodium hydroxide aqueous solution (dissolved sodium hydroxide with 30kg water) for gelatinization; then add aluminum sulfate, mix and stir at 68°C for 28 Minutes, and mixed with 280kg of cold water, stirred evenly; (3) Preparation of component C: dissolve 4kg of potassium pyroantimonate in another container with 20kg of water, then dilute with 900kg of water at 32°C, add borax and 550kg of cornstarch, Mix ...
Embodiment 3
[0022] Materials and proportions: corn starch 370kg, potassium pyroantimonate 2kg, dehydrated alum 15kg, light magnesium oxide 15kg, borax 10kg, solid sodium hydroxide 16kg, aluminum sulfate 0.6kg, polyvinyl alcohol 8kg, baking soda 2kg, water 1295kg .
[0023] Preparation: (1) Prepare component A: put the dehydrated alum into a drying furnace, raise the temperature to 135° C., after drying, drop to normal temperature and discharge, crush and sieve, and mix evenly with light magnesium oxide; (2) Prepare component B: add 70kg cornstarch to 120kg water to prepare starch slurry; add sodium hydroxide aqueous solution (dissolved sodium hydroxide with 35kg water) for gelatinization; then add aluminum sulfate, mix and stir at 72°C for 32 Minutes, and mixed with 200kg of cold water, stirred evenly; (3) Preparation of component C: Dissolve potassium pyroantimonate in another container with 40kg of water, then dilute with 900kg of water at 37°C, add borax and 300kg of cornstarch, mix U...
PUM
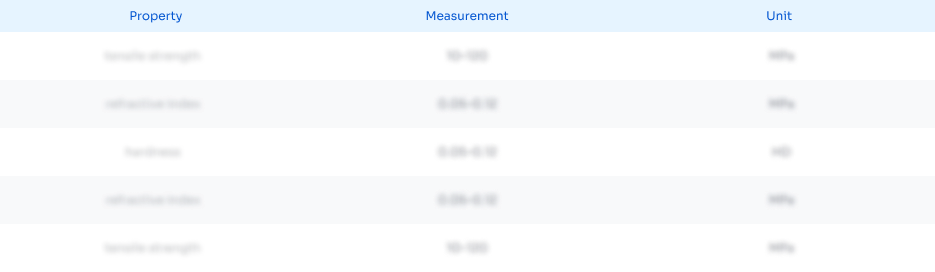
Abstract
Description
Claims
Application Information

- R&D Engineer
- R&D Manager
- IP Professional
- Industry Leading Data Capabilities
- Powerful AI technology
- Patent DNA Extraction
Browse by: Latest US Patents, China's latest patents, Technical Efficacy Thesaurus, Application Domain, Technology Topic, Popular Technical Reports.
© 2024 PatSnap. All rights reserved.Legal|Privacy policy|Modern Slavery Act Transparency Statement|Sitemap|About US| Contact US: help@patsnap.com