Double-phase opposition giant magnetostriction self-sensing drive direct force feedback servo valve
A giant magnetostrictive and self-sensing technology, applied in the field of servo control, can solve the problems of difficult to meet the requirements of the working bandwidth of the motor converter, poor anti-interference ability, and low energy density, so as to improve the motion accuracy and valve performance. The effects of control accuracy, system stability, and short response time
- Summary
- Abstract
- Description
- Claims
- Application Information
AI Technical Summary
Problems solved by technology
Method used
Image
Examples
Embodiment Construction
[0023] The present invention will be further described below in conjunction with accompanying drawing:
[0024] This embodiment is composed of two parts: the upper part is a double-phase opposing giant magnetostrictive self-sensing driver; the lower part is a power stage slide valve.
[0025]The function of the driver is to convert the input current signal into the deflection of the flexible hinged push rod. It includes an outer casing, an inner casing and an output assembly 10. The casing includes a casing 3 and end caps 2 fixed at both ends of the casing 3 . The inner sleeve includes an adjusting screw 1, a coil frame 7, a giant magnetostrictive rod 4, a driving coil 5, a bias coil 6, a coil frame 7, and a micro-displacement amplification mechanism 8, and forms a closed magnetic circuit, so that the magnetic flux generated in the coil Basically, they are confined in the magnetic circuit composed of magnetic materials, and the magnetic flux leakage is very small, which not ...
PUM
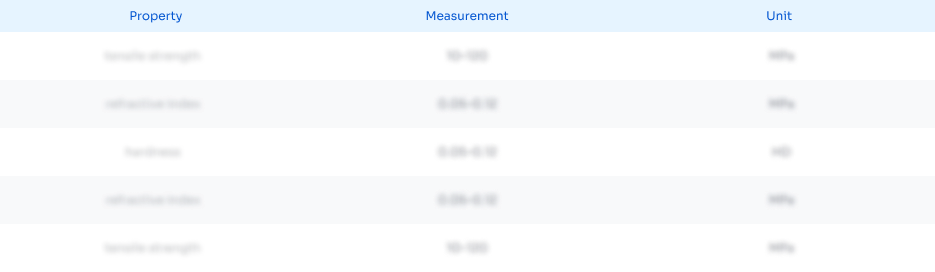
Abstract
Description
Claims
Application Information

- R&D Engineer
- R&D Manager
- IP Professional
- Industry Leading Data Capabilities
- Powerful AI technology
- Patent DNA Extraction
Browse by: Latest US Patents, China's latest patents, Technical Efficacy Thesaurus, Application Domain, Technology Topic, Popular Technical Reports.
© 2024 PatSnap. All rights reserved.Legal|Privacy policy|Modern Slavery Act Transparency Statement|Sitemap|About US| Contact US: help@patsnap.com