Investment casting method
A technology of investment casting and investment casting, which is applied in the direction of casting molding equipment, molds, mold components, etc., and can solve problems such as high cost, complicated materials, and long production cycle
- Summary
- Abstract
- Description
- Claims
- Application Information
AI Technical Summary
Problems solved by technology
Method used
Examples
Embodiment Construction
[0014] Design and manufacture the mold according to the part drawing, inject the prepared mold material (paste) with a certain temperature (paraffin, stearic acid) into the mold cavity through a certain equipment, and mold the mold material after cooling in the mold cavity. Take out the required part model, weld the wax model on the wax casting rod with a soldering iron to form a wax model group; prepare the slurry according to the process requirements, and evenly coat the outer surface of the wax model group with a layer of slurry; then apply the paint The surface of the module is uniformly sprinkled with a layer of sand particles of a certain specification; the module after sanding is soaked in the hardening solution in the pool to soak and harden; after a certain period of hardening in the pool, the module is hung on a shelf for water-controlled air-drying; finally Put the module into the pre-heated water to melt the wax mold in the shell; the above steps are repeated 3 time...
PUM
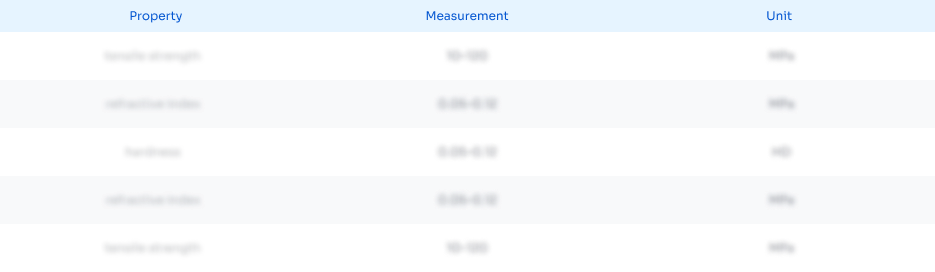
Abstract
Description
Claims
Application Information

- R&D
- Intellectual Property
- Life Sciences
- Materials
- Tech Scout
- Unparalleled Data Quality
- Higher Quality Content
- 60% Fewer Hallucinations
Browse by: Latest US Patents, China's latest patents, Technical Efficacy Thesaurus, Application Domain, Technology Topic, Popular Technical Reports.
© 2025 PatSnap. All rights reserved.Legal|Privacy policy|Modern Slavery Act Transparency Statement|Sitemap|About US| Contact US: help@patsnap.com