Preparation of calcium carbonate complex particle
A technology of composite particles and calcium carbonate, which is applied in chemical instruments and methods, inorganic pigment treatment, fibrous fillers, etc., can solve the problems of insufficient coating of calcium carbonate surface, difficult calcium carbonate particles, long processing time, etc. Improvement, simple operating conditions, and the effect of lowering the pH value
- Summary
- Abstract
- Description
- Claims
- Application Information
AI Technical Summary
Problems solved by technology
Method used
Image
Examples
Embodiment 1
[0023] This embodiment provides a preparation method for synthesizing calcium carbonate composite particles, which can prepare a calcium carbonate particle with strong acid resistance, such as figure 1 As shown, the specific preparation method is as follows:
[0024] In the calcium carbonate slurry with a concentration of 5% to 20%, add water glass solution, and SiO in the added water glass solution 2 and the CaCO in the calcium carbonate slurry 3 The mass ratio of the calcium carbonate slurry is 5 to 25%, and a dispersing aid can also be added to the calcium carbonate slurry at the same time. The amount of the dispersing aid added is 0.1 to 3% of the weight of the calcium carbonate slurry, and the mixed slurry is heated to 80-80%. 90°C, under the state of vigorous stirring (generally refers to the stirring state of the stirring device reaching 1000 rpm to 1500 rpm) for 1 to 1.5 hours, after the reaction, add a pH regulator to adjust the pH value of the slurry to 8 to 10 , k...
Embodiment 2
[0028] The present embodiment provides a kind of preparation method of calcium carbonate composite particle, can prepare the calcium carbonate particle with strong acid resistance, this calcium carbonate composite particle can be used in a wider range, and specific preparation process is as follows:
[0029] In the calcium carbonate slurry that the concentration is 15%, add water glass solution, add the consumption of water glass solution with the SiO in water glass solution 2 with the CaCO in the calcium carbonate slurry 3 The mass ratio of the mixture is 15%, the mixed slurry is heated to 85°C, and under vigorous stirring (generally refers to stirring at a state of 1000 rpm to 1500 rpm), use ethyl acetate as a pH regulator Adjust the pH value of the slurry to 8.5, age at 85°C for 3 hours, wash and filter, and dry at 130°C after washing for 60 minutes. After drying, crush to obtain calcium carbonate composite particle.
Embodiment 3
[0031] This embodiment provides a preparation method of calcium carbonate composite particles, which can well prepare calcium carbonate particles with strong acid resistance. The specific preparation process is as follows:
[0032] In the calcium carbonate slurry that the concentration is 20%, add water glass solution, add the consumption of water glass solution with the SiO in water glass solution 2 with the CaCO in the calcium carbonate slurry 3 The mass ratio is 5%, the mixed slurry is heated to 80 ° C, under vigorous stirring, the addition of CO as a pH regulator 2 Adjust the pH value of the slurry to 9-10, age at a constant temperature of 80°C for 3 hours, wash and filter, dry at 130°C for 50 minutes after washing, and pulverize after drying to obtain calcium carbonate composite particles.
PUM
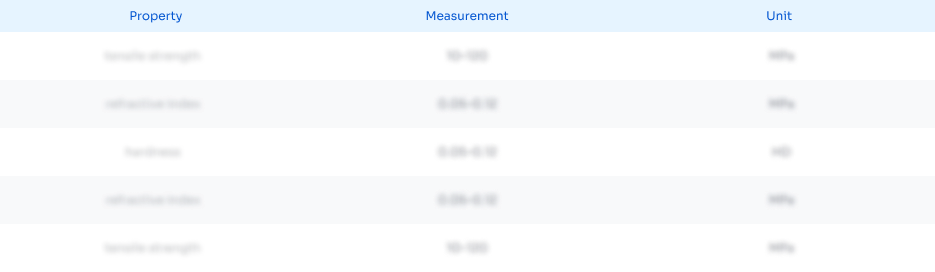
Abstract
Description
Claims
Application Information

- R&D Engineer
- R&D Manager
- IP Professional
- Industry Leading Data Capabilities
- Powerful AI technology
- Patent DNA Extraction
Browse by: Latest US Patents, China's latest patents, Technical Efficacy Thesaurus, Application Domain, Technology Topic, Popular Technical Reports.
© 2024 PatSnap. All rights reserved.Legal|Privacy policy|Modern Slavery Act Transparency Statement|Sitemap|About US| Contact US: help@patsnap.com