Composite amine antioxidant, preparation and use thereof
An antioxidant, complex amine technology, applied in chemical instruments and methods, compositions for inhibiting chemical changes, etc., can solve the problems of complex operating conditions, easy polymerization, difficult control, etc., to simplify operating conditions and improve comprehensive performance. , the effect of reducing the content of free amines
- Summary
- Abstract
- Description
- Claims
- Application Information
AI Technical Summary
Problems solved by technology
Method used
Image
Examples
Embodiment 1
[0033] In a 250ml autoclave, add 33.8 grams (0.2mol) of diphenylamine, 21.9 grams (0.1mol) of phenyl-α-naphthylamine, 50.4 grams (0.45mol) of diisobutylene, 2 grams of neutral clay and AlCl 3 Composite catalyst, 20ppm hydroquinone polymerization inhibitor, three reaction systems replaced with nitrogen. Heat to 170°C for reaction, start stirring at 100°C at 200 rpm. The reaction pressure was 0.30MPa, and the pressure gradually decreased to 0.17MPa as the reaction progressed. After the reaction was carried out for 10 hours, the material was cooled and transferred to a 250ml three-necked flask, heated and vacuum distilled at a residual pressure of 60mmHg and a temperature of 140°C for 20 minutes. Remove unreacted diisobutene starting material and a small amount of water. Then the material temperature was lowered to 120° C., and the catalyst waste residue was removed by filtration. 86.34 g of reddish-brown liquid viscous product were obtained.
Embodiment 2
[0035] Add 25.4 grams (0.15mol) of diphenylamine, 32.8 grams (0.15mol) of phenyl-α-naphthylamine, 67.2 grams (0.6mol) of diisobutylene, 5 grams of neutral clay and AlCl in a 250ml autoclave 3 Composite catalyst, 20ppm hydroquinone polymerization inhibitor, three reaction systems replaced with nitrogen. Heat up to 175°C for reaction, start stirring when the temperature is 100°C, and the rotation speed is 200 rpm. The reaction pressure was 0.38MPa, and the pressure gradually decreased to 0.15MPa as the reaction progressed. After the reaction was carried out for 12 hours, the material was cooled and transferred to a 250ml three-necked flask, heated and vacuum distilled at a residual pressure of 60mmHg and a temperature of 140°C for 20 minutes. Remove unreacted diisobutene starting material and a small amount of water. Then the material temperature was lowered to 120° C., and the catalyst waste residue was removed by filtration. 91.93 g of reddish-brown liquid viscous product we...
Embodiment 3
[0037] In a 250ml stainless steel autoclave, add 8.45 grams (0.05mol) of diphenylamine, 54.75 grams (0.25mol) of phenyl-α-naphthylamine, 39.2 grams (0.35mol) of diisobutylene, 8 grams of neutral clay and AlCl 3 Composite catalyst, 30ppm hydroquinone polymerization inhibitor, three reaction systems replaced with nitrogen. Heating to 180°C for reaction, and stirring at a temperature of 100°C at a speed of 200 rpm. The reaction pressure is 0.30MPa, and the pressure is gradually reduced to 0.18MPa along with the reaction. After the reaction is carried out for 2 hours, 11.2 grams (0.1mol) of diisobutylene is added by a metering pump, and the temperature is kept to continue the reaction. After the reaction is carried out for 4 hours, 11.2 grams of diisobutylene are added. (0.1mol) diisobutene, keep the temperature and continue the reaction. After the reaction is over for 7 hours, cool the material and transfer it to a 250ml three-necked flask. At a residual pressure of 60mmHg and a ...
PUM
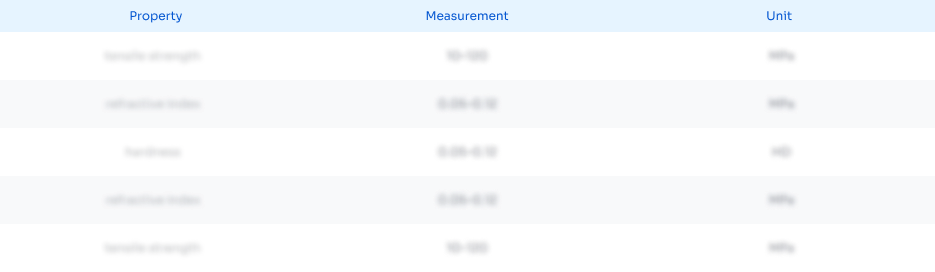
Abstract
Description
Claims
Application Information

- R&D
- Intellectual Property
- Life Sciences
- Materials
- Tech Scout
- Unparalleled Data Quality
- Higher Quality Content
- 60% Fewer Hallucinations
Browse by: Latest US Patents, China's latest patents, Technical Efficacy Thesaurus, Application Domain, Technology Topic, Popular Technical Reports.
© 2025 PatSnap. All rights reserved.Legal|Privacy policy|Modern Slavery Act Transparency Statement|Sitemap|About US| Contact US: help@patsnap.com