Process for preparing cobalt boracylate by hybrid reaction of cobaltous carbonate and organic carboxyl acid
A preparation process, organic carboxylic acid technology, applied in cobalt organic compounds, organic chemistry, chemical instruments and methods, etc., can solve the problem of reducing the adhesion stability of rubber and steel wire, unfavorable rubber and steel wire adhesion, and high total acidity of free fatty acids. problems, to achieve the effect of maintaining stability, preventing metal rust, and improving heat-resistant oxygen
- Summary
- Abstract
- Description
- Claims
- Application Information
AI Technical Summary
Problems solved by technology
Method used
Image
Examples
Embodiment 1
[0042] Add 60g of glacial acetic acid, 70g of neodecanoic acid, 34g of isooctanoic acid, and 100g of cobalt carbonate to a 1000ml four-necked flask equipped with a reflux condenser, a temperature-regulating electric heating mantle, and a vacuum pump, and control the reaction temperature at 105°C. Drain to remove the water formed by the reaction. Add 60g of dibutyl borate at a temperature of 170°C, the reaction time is 2 hours, heat up and drain, vacuum depressurize and drain, discharge butyl acetate, add 16g of active calcium carbonate and 20g of resin acid at a temperature of 180°C, and evenly After stirring for 1 hour, the materials were discharged to obtain the cobalt boroacylate product. The prepared cobalt boroacylate has a cobalt content of 22.7% and a blue-purple appearance.
Embodiment 2
[0044] Add 64g of glacial acetic acid, 74g of neodecanoic acid, 36g of isooctanoic acid, and 98g of cobalt carbonate to a 1000ml four-neck flask equipped with a reflux condenser, a temperature-regulating electric heating mantle, and a vacuum pump in sequence, and control the reaction temperature at 100°C. The reaction time is 4 hours, and the temperature is raised. Drain, remove the water generated by the reaction, add 64g of tributyl borate at a temperature of 160°C, react for 2.5 hours, heat up and drain, vacuum and reduce pressure, drain butyl acetate, add active calcium carbonate at 175°C 18g, 24g of resin acid, stirred evenly for 1 hour, and discharged to obtain a cobalt boroacylate product with a cobalt content of 22.5% and a blue-purple appearance.
Embodiment 3
[0046] Add 62g of glacial acetic acid, 73g of neodecanoic acid, 38g of isooctanoic acid, and 96g of cobalt carbonate into a 1000ml four-neck flask with a reflux condenser, a temperature-regulating electric heating mantle, and a vacuum pump in sequence, and control the reaction temperature at 110°C. Drain, remove the water generated by the reaction, add 62g of tributyl borate at a temperature of 180°C, react for 3 hours, heat up and drain, vacuum and reduce pressure, drain butyl acetate, add active calcium carbonate at 185°C 20g and 22g of resin acid were stirred evenly for 1 hour and discharged to obtain a cobalt boroacylate product with a cobalt content of 22.1% and a blue-purple appearance.
PUM
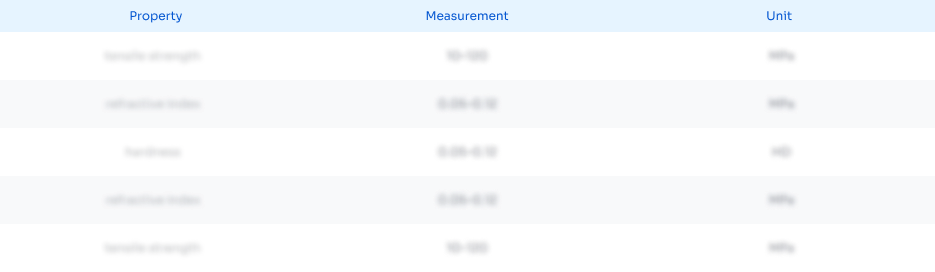
Abstract
Description
Claims
Application Information

- R&D Engineer
- R&D Manager
- IP Professional
- Industry Leading Data Capabilities
- Powerful AI technology
- Patent DNA Extraction
Browse by: Latest US Patents, China's latest patents, Technical Efficacy Thesaurus, Application Domain, Technology Topic, Popular Technical Reports.
© 2024 PatSnap. All rights reserved.Legal|Privacy policy|Modern Slavery Act Transparency Statement|Sitemap|About US| Contact US: help@patsnap.com