Machine for manufacturing frame of a fan
A technology for making machine and fan bones, which is applied in wood stamping, wood compression, etc., can solve the problems that the mechanized stamping and forming of fan bones cannot be realized, and achieve the effect of improving the quality of fan bone forming, getting rid of the dependence of workers on craftsmanship, and improving safety
- Summary
- Abstract
- Description
- Claims
- Application Information
AI Technical Summary
Problems solved by technology
Method used
Image
Examples
Embodiment 1
[0040] Referring to the attached picture:
[0041] The fan bone making machine of the present invention comprises a stamping machine 21, a frame 10, a base plate 5 provided with a bamboo chip conveying channel 1, and the bamboo chip conveying channel 1 is connected to the stamping station on the stamping machine, and the stamping station is equipped with a The female mold 25 and male mold 24 of fan bone.
[0042] A slice mechanism, a midway positioning mechanism, and a secondary conveying mechanism are sequentially arranged on the bamboo slice conveying channel 1 .
[0043] The fragmentation mechanism described includes:
[0044] A storage tank 2 for stacking bamboo chips is arranged above the bamboo chip conveying channel 1 , and the opening at the bottom of the storage tank 2 is adapted to the bamboo chip and aligned with the bamboo chip conveying channel 1 . The opening at the bottom of the storage tank 2 is arranged transversely with respect to the bamboo chip conveying ...
Embodiment 2
[0059] Present embodiment increases on the halfway positioning mechanism: the bottom surface of step 19 is provided with the 3rd air suction port 26, and the 3rd air suction port 26 is distributed in the middle part and both sides of the bamboo sheet transmission passage, the 3rd air suction port 26 connects all The negative pressure source described above. Elastic pressure sheet 20 is equipped with on the top of step 19. The third suction port 26 and the elastic pressing sheet 20 can all reduce the jumping and shaking of the bamboo chips, help the bamboo chips to be positioned accurately and maintain balance, and create conditions for the secondary conveying mechanism to accurately send the bamboo chips into the stamping station at last.
[0060] Others are the same as in Example 1.
Embodiment 3
[0062] The special added measures of this embodiment are: the bottom of the front end of the middle fork 7 has a notch 27 for inserting the bamboo slice, and the height of the notch 27 is suitable for the bamboo slice.
[0063] Can make middle fork 7 like this when pushing away bamboo slice 16, suppress bamboo slice 16, prevent it from jumping, rocking.
[0064] Others are identical with embodiment 2.
PUM
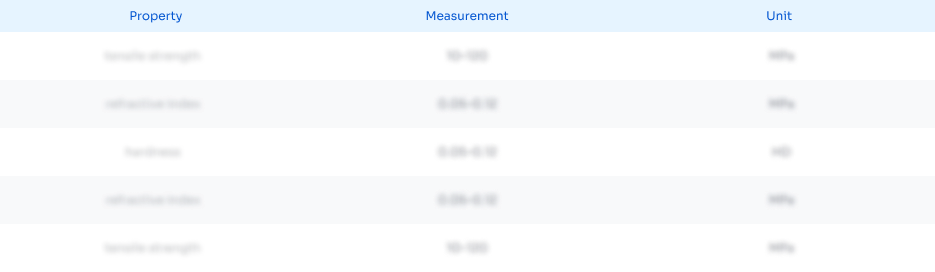
Abstract
Description
Claims
Application Information

- R&D
- Intellectual Property
- Life Sciences
- Materials
- Tech Scout
- Unparalleled Data Quality
- Higher Quality Content
- 60% Fewer Hallucinations
Browse by: Latest US Patents, China's latest patents, Technical Efficacy Thesaurus, Application Domain, Technology Topic, Popular Technical Reports.
© 2025 PatSnap. All rights reserved.Legal|Privacy policy|Modern Slavery Act Transparency Statement|Sitemap|About US| Contact US: help@patsnap.com