Smelting production method of low activation martensitic steel for fusion reactor
A martensitic steel and production method technology, applied in the field of metal material processing, can solve the problems of inability to prepare qualified CLAM steel, difficult to achieve precise control of composition, difficult to control requirements of impurity elements, etc., and achieve large-scale industrialization The effect of production, low inclusion levels and high process repeatability
- Summary
- Abstract
- Description
- Claims
- Application Information
AI Technical Summary
Problems solved by technology
Method used
Image
Examples
Embodiment Construction
[0035] By adopting the process of the present invention, qualified CLAM steel is prepared, and the mass fractions of each component are: Cr: 8.5-9.5%, W 1.3-1.7%, V 0.15-0.25%, Ta 0.12-0.18%, Mn 0.40~0.50%, C0.08~0.12%, the specific smelting and preparation process is as follows:
[0036] Step 1: Melting charge in a vacuum induction furnace:
[0037] 1. Put pure iron into the furnace, put the alloy raw material into the vacuum alloy hopper;
[0038] 2. First add pure metal Cr and W raw materials into the vacuum induction furnace, heat up and vacuumize, the melting temperature is about 1500-1600°C, and the vacuum degree reaches 5-10Pa;
[0039] 3. After the raw materials in the furnace are partially melted, stop the vacuuming, pass in Ar gas to 0.05MPa for protection, and add pure metal V and Ta after melting. After the alloy is melted, depending on the condition of the molten pool, the vacuum is gradually evacuated to below 0.1-10Pa and kept for 3-10min;
[0040] 4. Add pur...
PUM
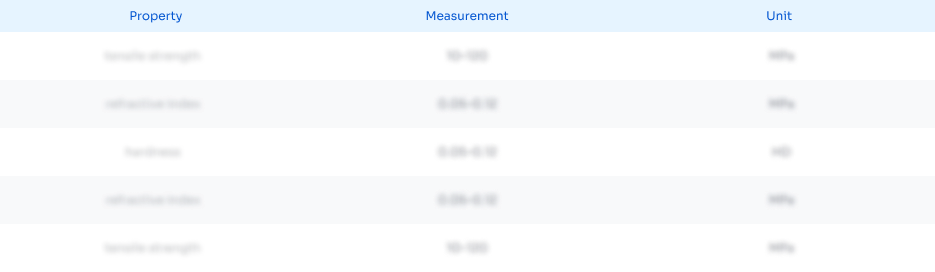
Abstract
Description
Claims
Application Information

- R&D
- Intellectual Property
- Life Sciences
- Materials
- Tech Scout
- Unparalleled Data Quality
- Higher Quality Content
- 60% Fewer Hallucinations
Browse by: Latest US Patents, China's latest patents, Technical Efficacy Thesaurus, Application Domain, Technology Topic, Popular Technical Reports.
© 2025 PatSnap. All rights reserved.Legal|Privacy policy|Modern Slavery Act Transparency Statement|Sitemap|About US| Contact US: help@patsnap.com