Dry coal powder airflow bed gasification furnace
A technology of entrained bed and dry coal powder, which is applied in the direction of granular/powdered fuel gasification, etc., can solve the problems of gasification reaction area deviation, increase the average temperature level of the upper furnace body, etc., achieve complete gasification reaction and improve gasification Efficiency, increased contact and reaction time effects
- Summary
- Abstract
- Description
- Claims
- Application Information
AI Technical Summary
Problems solved by technology
Method used
Image
Examples
Embodiment Construction
[0023] see figure 1 , the outer wall 9 of the gasification furnace is an upright cylinder, and the internal structure is composed of the main gasification chamber 13 in the upper section and the quenching chamber 14 in the lower section.
[0024] The main gasification chamber 13 in the upper section is a water-cooled wall structure, which is surrounded by a coil-type water-cooled wall 7 , a refractory insulation layer 8 and an outer wall 9 from the inside to the outside. On the upper part of the main gasification chamber 13, there are two first-stage pulverized coal nozzles 11 of the center-to-spray type and two two first-stage gasification agent nozzles 10 parallel to the first-stage pulverized coal nozzles 11 and offset to each other by a certain distance, see figure 2 , the offset is the inner diameter of the main gasification chamber 13 Arrange two secondary pulverized coal nozzles 12 and two secondary gasifying agent nozzles 16 in the middle of the main gasification ch...
PUM
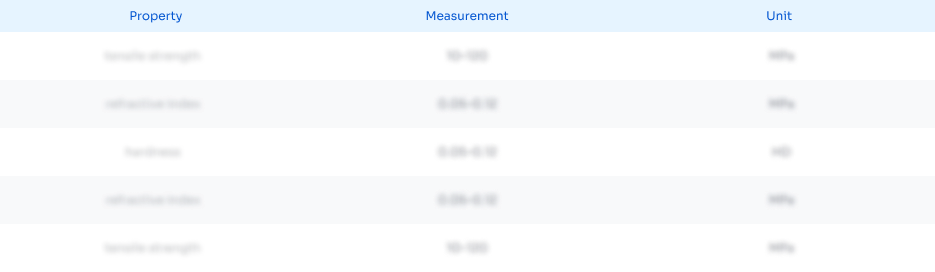
Abstract
Description
Claims
Application Information

- R&D Engineer
- R&D Manager
- IP Professional
- Industry Leading Data Capabilities
- Powerful AI technology
- Patent DNA Extraction
Browse by: Latest US Patents, China's latest patents, Technical Efficacy Thesaurus, Application Domain, Technology Topic, Popular Technical Reports.
© 2024 PatSnap. All rights reserved.Legal|Privacy policy|Modern Slavery Act Transparency Statement|Sitemap|About US| Contact US: help@patsnap.com