Preparing technological process of laser aluminum plating paper
A technology of laser aluminum plating and preparation process, which is applied in the printing process, the process for producing decorative surface effects, and the printing of special varieties of printed matter, which can solve the problem of long de-labeling time for recycled bottles, low productivity and waste in the bottle washing process. Heating alkaline solution and other problems, to achieve good lye permeability, facilitate natural degradation, and be conducive to the effect of environmental protection
- Summary
- Abstract
- Description
- Claims
- Application Information
AI Technical Summary
Problems solved by technology
Method used
Examples
Embodiment 1
[0040] Embodiment 1, a kind of preparation technology method of laser aluminized paper, comprises the following steps:
[0041] Coating release layer on the OPP film, wherein used coating polyurethane emulsion 40%, acrylic acid emulsion 12.5%, deionized water 17.5%, isopropanol 30% weight ratio preparation, resin solid part accounts for the weight percent of coating in the coating is 15%;
[0042] When coating the release layer, the release layer coating is uniformly and quantitatively coated on the film by using a roller coating method, and the speed of the coating process is 100 m / min.
[0043] The coated film was dried in an oven at 115°C, and the dry coating weight was 1.4g / m 2 , the oven drying adopts the compound drying method of far-infrared drying and heating air matching the far-infrared wavelength;
[0044] The imaging layer is coated on the peeling layer. The coating of the imaging layer includes acrylic resin and cellulose acetate butyl cellulose resin. Contain ...
Embodiment 2
[0051] Embodiment 2, a kind of preparation technology method of laser aluminized paper, first on PET film coating release layer, release layer coating comprises polyurethane emulsion 35%, acrylic acid emulsion 15%, deionized water 25%, isopropanol 25% , wherein the resin solid content accounts for 5% by weight of the coating. When coating the release layer, the roll coating method is adopted to uniformly and quantitatively coat the release layer coating on the film. The speed of the coating process is 120 meters per minute. After drying in an oven at 80°C, the oven drying adopts a composite drying method of far-infrared drying and heating air that matches the wavelength of far-infrared rays. The dry coating amount is 0.4g / m 2 ;
[0052] Then on the release layer, the imaging layer is coated, and the imaging layer coating comprises 0.5% cellulose acetate resin, 99.5% acrylic resin; the weight proportion of the solvent is 20% butanone, 70% ethyl acetate, 10% isopropanol, The re...
Embodiment 3
[0060] Embodiment 3, a kind of preparation technology method of laser aluminized paper, at first on PET film coating peel-off layer, peel-off layer coating comprises, polyurethane emulsion 47.5%, acrylic acid emulsion 2.5%, deionized water 25%, isopropanol 25% %, wherein the resin solid content accounts for 25% by weight of the coating. When coating the peeling layer, the roller coating method is adopted to uniformly and quantitatively coat the peeling layer coating on the film. The speed of the coating process is 120 m / min , after being dried in an oven at 180°C, the oven drying adopts a composite drying method of far-infrared drying and heating air that matches the wavelength of far-infrared rays, and the dry coating amount is 1.4g / m 2 ;
[0061] Then on the release layer, the imaging layer is coated, and the imaging layer coating comprises 30% of cellulose acetate resin and 70% of acrylic resin; The resin is prepared by dissolving and dispersing in a solvent, and the solid...
PUM
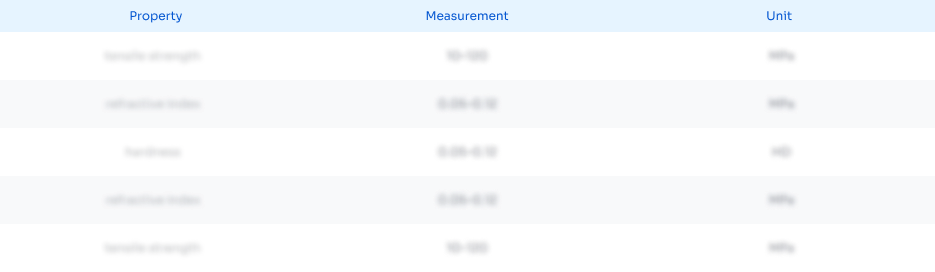
Abstract
Description
Claims
Application Information

- R&D
- Intellectual Property
- Life Sciences
- Materials
- Tech Scout
- Unparalleled Data Quality
- Higher Quality Content
- 60% Fewer Hallucinations
Browse by: Latest US Patents, China's latest patents, Technical Efficacy Thesaurus, Application Domain, Technology Topic, Popular Technical Reports.
© 2025 PatSnap. All rights reserved.Legal|Privacy policy|Modern Slavery Act Transparency Statement|Sitemap|About US| Contact US: help@patsnap.com