Method for eliminating residual polymer of etching procedure
A polymer and etching technology, applied in the direction of electrical components, semiconductor/solid-state device manufacturing, circuits, etc., to achieve the effect of easy realization, elimination of crown defects, and increase of production costs
- Summary
- Abstract
- Description
- Claims
- Application Information
AI Technical Summary
Problems solved by technology
Method used
Image
Examples
Embodiment Construction
[0014] The process tools used in the semiconductor etching process include a main etch reaction chamber (chamber) for main etching (Main Etch), and a stripping reaction chamber for stripping (strip). Among them, the main etching step removes most of the polysilicon without damaging the gate oxide, and the stripping step removes the previously used resist protection film.
[0015] see figure 1 , is a schematic flow chart of a conventional semiconductor etching process. It proceeds from the main etching step in the main etching reaction chamber to the stripping step in the stripping reaction chamber, at this time, the polymer is produced on the sidewall.
[0016] Generally, etching techniques can be classified into wet etching and dry etching. In wet etching, a chemical solution is used to achieve the purpose of etching through a chemical reaction; dry etching is generally called plasma etching (Plasma Etching). Plasma is a phenomenon in which gas molecules are in a Breakdow...
PUM
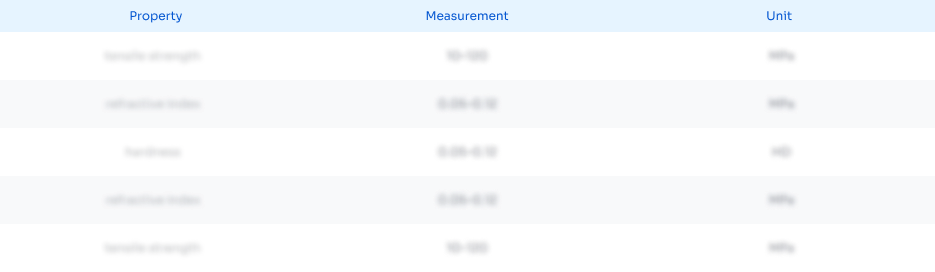
Abstract
Description
Claims
Application Information

- R&D
- Intellectual Property
- Life Sciences
- Materials
- Tech Scout
- Unparalleled Data Quality
- Higher Quality Content
- 60% Fewer Hallucinations
Browse by: Latest US Patents, China's latest patents, Technical Efficacy Thesaurus, Application Domain, Technology Topic, Popular Technical Reports.
© 2025 PatSnap. All rights reserved.Legal|Privacy policy|Modern Slavery Act Transparency Statement|Sitemap|About US| Contact US: help@patsnap.com