Pneumatic belt tire
A technology for radial tires and tires, which is applied to the reinforcement layer of pneumatic tires, tire parts, tire treads/tread patterns, etc. To avoid layer bending and other problems, achieve the effect of maintaining cost competitiveness and improving partial wear performance
- Summary
- Abstract
- Description
- Claims
- Application Information
AI Technical Summary
Problems solved by technology
Method used
Image
Examples
Embodiment 1
[0039] has been trial-produced with figure 1 A tire with the tread pattern shown and a 2-steel belt structure that satisfies the following conditions.
[0040] Tire size specification: 155 / 65R13 73S
[0041] Tread width TW: 120mm
[0042] The ratio of pattern groove to pattern block area (negative rate): 32%
[0043] Width of circumferential main groove 1a: 18mm, width of 1b: 9.1mm
[0044] Depth of circumferential main grooves 1a, 1b: 6.0mm
[0045] The width of the part of the transverse groove 2 connected with the circumferential main groove 1b: 2.5 ~ 4.5mm (varies with the pitch)
[0046] Depth of transverse groove 2: 5mm
[0047] Width w of the ground portion L: 5mm
[0048] Width of intermittent slit auxiliary groove 3: 1.5mm
[0049] Depth of intermittent gap auxiliary groove 3: 5mm
[0050] Radius of curvature R1: 1000mm
[0051] Radius of curvature R2: 5mm
[0052] Conventional Example 1
[0053] use has image 3 A known tire having the tread pattern and...
Embodiment 2
[0070] Trial out: In addition to having Figure 4 A tire having one belt reinforcement layer in addition to the tread pattern and two-wire belt structure shown, and satisfying the following conditions.
[0071] Tire size specification: 195 / 65R15 91H
[0072] Tread width TW: 140mm
[0073] Groove to block area ratio: 34%
[0074] Width of circumferential main groove 1a: 9mm, width of 1b: 10.5mm
[0075] Depth of circumferential main grooves 1a, 1b: 7.5mm
[0076] Width of the portion of the transverse groove 2 communicating with the circumferential main groove 1b: 2.5 to 4.5 mm (varies with the pitch)
[0077] Depth of transverse groove 2: 5mm
[0078] Width w of the ground portion L: 5mm
[0079] Width of intermittent slit auxiliary groove 3: 2mm
[0080] Depth of intermittent slit auxiliary groove 3: 6mm
[0081] Radius of curvature R1: 145mm
[0082] Radius of curvature R2: 36mm
[0083] Conventional example 2
[0084] Adopted in previous example 2: with Figur...
PUM
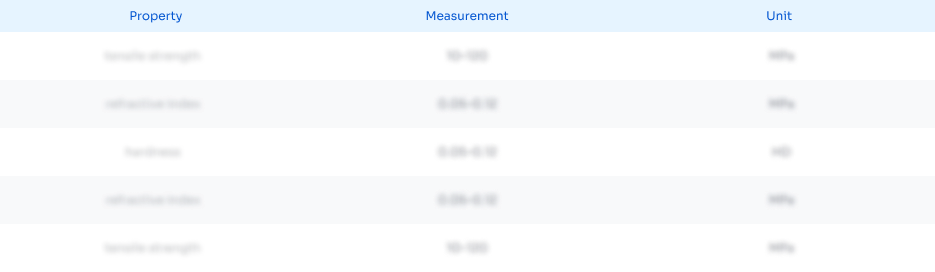
Abstract
Description
Claims
Application Information

- R&D
- Intellectual Property
- Life Sciences
- Materials
- Tech Scout
- Unparalleled Data Quality
- Higher Quality Content
- 60% Fewer Hallucinations
Browse by: Latest US Patents, China's latest patents, Technical Efficacy Thesaurus, Application Domain, Technology Topic, Popular Technical Reports.
© 2025 PatSnap. All rights reserved.Legal|Privacy policy|Modern Slavery Act Transparency Statement|Sitemap|About US| Contact US: help@patsnap.com