Ultra-dispersed composite stabilizer for polychloroethylene and preparation thereof
A composite stabilizer and polyvinyl chloride technology, which is applied in the field of composite stabilizers, can solve problems such as the application of hyperdispersants, achieve excellent synergistic stabilization effects, reduce batching procedures, and reduce batching errors.
- Summary
- Abstract
- Description
- Claims
- Application Information
AI Technical Summary
Problems solved by technology
Method used
Image
Examples
Embodiment 1
[0026] Add a certain amount of polyethylene glycol, dodecylbenzenesulfonic acid, and hydroquinone into the three-necked flask, start adding acrylic acid at 110-120°C, and keep the temperature at 120°C for 2.5 hours after the dropwise addition. Evaporate the by-product water from the reaction liquid under reduced pressure, react at this temperature for 2 hours, and the speed of dehydration will be significantly slowed down; keep the temperature at 130°C until the amount of water obtained by the vacuum reaction is close to the theoretical value, which is the end point of the reaction; under vacuum conditions Lower the temperature to below 40°C, and discharge the finished product.
[0027] The mass ratio of acrylic acid and polyethylene glycol is 1:0.8, dodecylbenzenesulfonic acid is 1.2% of the total amount of acrylic acid and polyethylene glycol, and hydroquinone is 0.5% of the total amount of acrylic acid and polyethylene glycol .
[0028] The second step is the preparation o...
Embodiment 2
[0031] In the 2m equipped with stirrer, thermometer and heating mantle 3 In the stainless steel reactor, add 800kg stearic acid, be warming up to 110 ℃, slowly add 100kg yellow lead and 20kg hyperdispersant (prepared in embodiment 1). After stirring and keeping warm for 30 minutes, add 80kg of monoglyceride, 6kg of polyethylene wax, and 340kg of light calcium carbonate in sequence. Continue to add 360kg three salts and 200kg two salts again. Keep warm at 110°C. After the material is evenly stirred, release the material to obtain the product. It can also be further granulated (or tableted) to form a granular (or flake) product. See formula table 1 for detailed formula, formula number JS-101.
Embodiment 3
[0033]In the 2m equipped with stirrer, thermometer and heating mantle 3 In the stainless steel reactor, add 700kg stearic acid, be warming up to 110 ℃, slowly add 100kg yellow lead and 30kg hyperdispersant (prepared in embodiment 1). After stirring and keeping warm for 30 minutes, add 100kg of barium stearate, and then add 6kg of polyethylene wax and 500kg of light calcium carbonate in sequence after the reaction is complete. Then continue to add 300kg three salts and 200kg two salts. Keep warm at 110°C. After the material is evenly stirred, release the material to obtain the product. It can also be further granulated (or tableted) to form a granular (or flake) product. See formula table 1 for detailed formula, formula number JS-102.
PUM
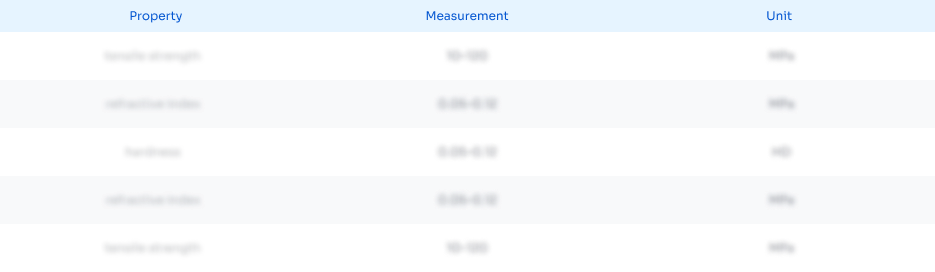
Abstract
Description
Claims
Application Information

- R&D
- Intellectual Property
- Life Sciences
- Materials
- Tech Scout
- Unparalleled Data Quality
- Higher Quality Content
- 60% Fewer Hallucinations
Browse by: Latest US Patents, China's latest patents, Technical Efficacy Thesaurus, Application Domain, Technology Topic, Popular Technical Reports.
© 2025 PatSnap. All rights reserved.Legal|Privacy policy|Modern Slavery Act Transparency Statement|Sitemap|About US| Contact US: help@patsnap.com