Trickle bed reactor
A reactor and trickle bed technology, applied in the field of trickle bed reactors, can solve the problems of poor trickle effect, uneven gas-liquid distribution, low catalytic reaction efficiency, etc. effect, the effect of improving the reaction efficiency
- Summary
- Abstract
- Description
- Claims
- Application Information
AI Technical Summary
Problems solved by technology
Method used
Image
Examples
Embodiment 1
[0022] As shown in Figure 1, the initial pyrolysis gasoline C 5 ~C 9 Fractions (oils) with a diene value greater than 25 g I 2 / 100 grams of Oil, hydrogen enters the trickle bed reactor with a hydrogen-oil ratio equal to 100, the catalyst adopts a general-purpose palladium series hydrogenation catalyst, adopts the trickle bed reactor of the present invention, and the gas-liquid distributor 3 is located below the feed port 1 800 millimeters, be positioned at the top 1000 millimeters of upper ceramic ball bed layer 4; The upper end of short pipe 13 stretches out 50 millimeters above distribution plate 8, and the lower end stretches out 500 millimeters below distribution plate 8, and the diameter d of aperture 14 and liquid channel pipe 10 The ratio of the inner diameter D is 0.015:1.0, the area S of all small holes 14 1 and the area S of the inner cross-section of the liquid channel tube 10 2 The ratio of the ratio is 1.01:1.0; the opening ratio of the gas passage pipe 9 on t...
Embodiment 2
[0024] As shown in Figure 1, the initial pyrolysis gasoline C 5 ~C 9 Fractions (oils) with a diene value greater than 25 g I 2 / 100 grams of Oil, hydrogen enters the trickle bed reactor with a hydrogen-oil ratio equal to 100, the catalyst adopts a general-purpose palladium series hydrogenation catalyst, adopts the trickle bed reactor of the present invention, and the gas-liquid distributor 3 is located below the feed port 1 500 millimeters, be positioned at the top 800 millimeters of upper ceramic ball bed layer 4; The upper end of short pipe 13 stretches out 90 millimeters above distribution plate 8, and the lower end stretches out 800 millimeters below distribution plate 8, and the diameter d of aperture 14 and liquid channel pipe 10 The ratio of the inner diameter D is 0.011:1.0, the area S of all small holes 14 1 and the area S of the inner cross-section of the liquid channel tube 10 2 The ratio of the ratio is 0.95:1.0; the opening ratio of the gas passage tube 9 on the...
Embodiment 3
[0026] As shown in Figure 1, the initial pyrolysis gasoline C 5 ~C 9 Fractions (oils) with a diene value greater than 25 g I 2 / 100 grams of Oil, hydrogen enters the trickle bed reactor with a hydrogen-oil ratio equal to 100, the catalyst adopts a general-purpose palladium series hydrogenation catalyst, adopts the trickle bed reactor of the present invention, and the gas-liquid distributor 3 is located below the feed port 1 300 millimeters, 600 millimeters above the top of the upper ceramic ball bed layer 4; the upper end of the short pipe 13 stretches out 60 millimeters above the distribution plate 8, and the lower end stretches out 650 millimeters below the distribution plate 8, and the diameter d of the small hole 14 is the same as that of the liquid channel pipe 10 The ratio of the inner diameter D is 0.15:1.0, the area S of all small holes 14 1 and the area S of the inner cross-section of the liquid channel tube 10 2 The ratio is 1.1:1.0; the opening ratio of the gas p...
PUM
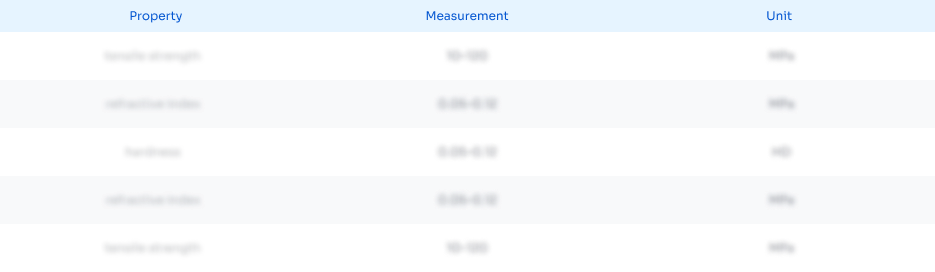
Abstract
Description
Claims
Application Information

- R&D Engineer
- R&D Manager
- IP Professional
- Industry Leading Data Capabilities
- Powerful AI technology
- Patent DNA Extraction
Browse by: Latest US Patents, China's latest patents, Technical Efficacy Thesaurus, Application Domain, Technology Topic, Popular Technical Reports.
© 2024 PatSnap. All rights reserved.Legal|Privacy policy|Modern Slavery Act Transparency Statement|Sitemap|About US| Contact US: help@patsnap.com