Hot rolling facility of steel plate and hot rolling method
A steel plate and equipment technology, which is applied in the hot rolling equipment and hot rolling field of steel plate, can solve the problems of uneven temperature, damaged cooling water film, easily damaged cooling water film 53, etc., and achieve excellent equipment cost, good cooling capacity, Excellent equipment maintenance effect
- Summary
- Abstract
- Description
- Claims
- Application Information
AI Technical Summary
Problems solved by technology
Method used
Image
Examples
Embodiment 1
[0057] As Example 1 of the present invention, controlled rolling on a hot rolling line for thick steel plates was performed. Here, after the sheet thickness was rolled to 28 mm, controlled rolling at a predetermined rolling temperature was performed in the last three passes.
[0058] At this time, as Example 1 of the present invention, in the 4 passes before the controlled rolling using the hot rolling facility ( FIG. 1 ) shown in the above-mentioned embodiment, the cooling facility provided on the entrance side and the exit side of the rolling mill 12 20. Rod-shaped cooling water is sprayed to cool the steel plate 10 so that the temperature of the steel plate 10 at the end of the 4th pass is rolled to a predetermined temperature, and then controlled rolling is performed in the last 3 passes.
[0059] Among them, set the depression angle θ of the upper nozzle 22 U is 45°, the elevation angle θ of the lower nozzle 32 L for 60
[0060] In addition, the inner diameters of the ...
Embodiment 2
[0075] As Example 2 of the present invention, rough rolling on a hot rolling line for thin steel sheets was performed. Here, the steel slab was rolled to a plate thickness of 42 mm by a rough rolling mill.
[0076] At this time, as Example 2 of the present invention, using the hot rolling facility ( FIG. 1 ) shown in the above-mentioned embodiment, in the three passes of rough rolling, from the cooling facility 20 provided on the entrance side and the exit side of the rolling mill 12 Rolling is performed while cooling the steel plate 10 by spraying rod-shaped cooling water. Among them, set the depression angle θ of the upper nozzle 22 U is 45°, the elevation angle θ of the lower nozzle 32 L is 60°. In addition, the inner diameters of the upper nozzle 22 and the lower nozzle 32 were 6 mm, and the injection speed of the rod-shaped cooling water was 8 m / s.
[0077] On the other hand, as Comparative Example 3, rough rolling was performed using a hot rolling facility not equipp...
Embodiment 3
[0091] As Example 3 of the present invention, finish rolling on a hot rolling line for thin steel sheets was performed. Here, rolling was carried out by the 7-stand finishing mill of F1 to F7 to a final plate thickness of 3 mm.
[0092] At this time, as Example 3 of the present invention, using the hot finish rolling facility ( FIG. 2 ) shown in the above-mentioned embodiment, in the 4 stands F4 to F7, the rod-shaped Rolling is performed while cooling water to cool the steel plate 10 . Among them, set the depression angle θ of the upper nozzle 22 U is 45°, the elevation angle θ of the lower nozzle 32 L is 60°. In addition, the inner diameters of the upper nozzle 22 and the lower nozzle 32 were 6 mm, and the injection speed of the rod-shaped cooling water was 8 m / s.
[0093] On the other hand, as Comparative Example 5, instead of the cooling facility 20 of Example 3 of the present invention, a hot rolling facility having the cooling facility described in JP 2002-361315 A wa...
PUM
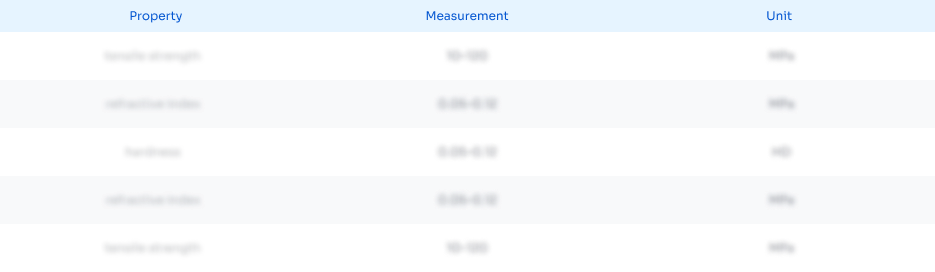
Abstract
Description
Claims
Application Information

- R&D
- Intellectual Property
- Life Sciences
- Materials
- Tech Scout
- Unparalleled Data Quality
- Higher Quality Content
- 60% Fewer Hallucinations
Browse by: Latest US Patents, China's latest patents, Technical Efficacy Thesaurus, Application Domain, Technology Topic, Popular Technical Reports.
© 2025 PatSnap. All rights reserved.Legal|Privacy policy|Modern Slavery Act Transparency Statement|Sitemap|About US| Contact US: help@patsnap.com