Developing spray nozzle structure and method for spraying developing solution
A developer and nozzle technology, applied in the direction of electrical components, semiconductor/solid-state device manufacturing, circuits, etc., can solve the problems of poor development, incomplete development, time-consuming and cost-effective, etc.
- Summary
- Abstract
- Description
- Claims
- Application Information
AI Technical Summary
Problems solved by technology
Method used
Image
Examples
Embodiment Construction
[0028] first as Figure 2A and Figure 2B As shown, it is a developing nozzle structure 20 according to a preferred embodiment of the present invention, which is suitable for a thin-film transistor liquid crystal display panel 200 to perform the developing process of the yellow light segment of the transistor array process, and the developing nozzle structure 20 mainly includes : nozzle cavity 22, several bubble discharge pipes 24, several injection pipes 26, an auxiliary injection pipe 27, several spraying pipes 28 and several gate devices 30.
[0029] The inside of the nozzle chamber 22 is divided into upper and lower parts by the several side-by-side gate devices 30, namely a first chamber 221 and a second chamber 223 below the first chamber 221. The purpose of its separation is to utilize liquid Different from the gas density, the gas floats upwards, so that the bubbles 212 generated when the developer 210 is injected will rise and concentrate in the first chamber 221 in ...
PUM
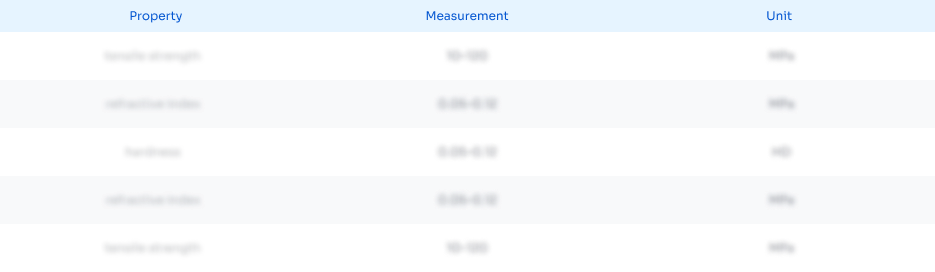
Abstract
Description
Claims
Application Information

- R&D Engineer
- R&D Manager
- IP Professional
- Industry Leading Data Capabilities
- Powerful AI technology
- Patent DNA Extraction
Browse by: Latest US Patents, China's latest patents, Technical Efficacy Thesaurus, Application Domain, Technology Topic, Popular Technical Reports.
© 2024 PatSnap. All rights reserved.Legal|Privacy policy|Modern Slavery Act Transparency Statement|Sitemap|About US| Contact US: help@patsnap.com