Formaldehyde oxidation reactor
An oxidation reactor and oxidizer technology, applied in chemical/physical/physical chemistry fixed reactor, oxidation to prepare carbonyl compounds, organic chemistry, etc., can solve the problem of unutilized process waste heat, reduced heat exchange efficiency, waste of heat energy, etc. To overcome the stress cracking phenomenon, solve the problem of stress corrosion, and improve the exchange efficiency
- Summary
- Abstract
- Description
- Claims
- Application Information
AI Technical Summary
Problems solved by technology
Method used
Image
Examples
Embodiment Construction
[0062] see first figure 1 The schematic diagram of the shown formaldehyde oxidation reactor of the present invention, the formaldehyde oxidation reactor of the present invention comprises:
[0063] top cover 22;
[0064] The oxidizer main cylinder 2 connected to the top cover 22 is provided with a catalyst layer 7 for oxidative dehydrogenation reaction to generate formaldehyde gas;
[0065] A device connected to the main cylinder body 2 of the oxidizer to output the generated formaldehyde gas, in this case, the device is a skirt 1 provided with a formaldehyde gas outlet 19;
[0066] It is characterized in that the top cover 22 includes:
[0067] The thermal insulation jacket 12 is composed of an inner cylinder 11 and an outer cylinder 23 that are sealed and connected, and a heating interlayer is formed between the outer cylinder 23 and the inner cylinder 11;
[0068] Enter the quaternary mixed gas inlet 8 inside the top cover 22 from the outer cylinder 23 and the inner cyl...
PUM
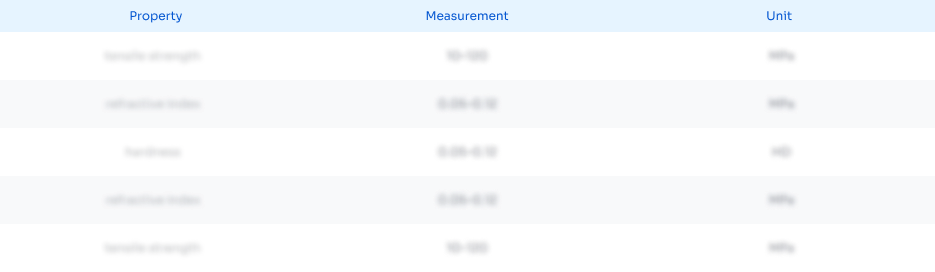
Abstract
Description
Claims
Application Information

- Generate Ideas
- Intellectual Property
- Life Sciences
- Materials
- Tech Scout
- Unparalleled Data Quality
- Higher Quality Content
- 60% Fewer Hallucinations
Browse by: Latest US Patents, China's latest patents, Technical Efficacy Thesaurus, Application Domain, Technology Topic, Popular Technical Reports.
© 2025 PatSnap. All rights reserved.Legal|Privacy policy|Modern Slavery Act Transparency Statement|Sitemap|About US| Contact US: help@patsnap.com