Self-cleaning reinforcement heat transfer low flow resistance rotor in heat-transfer pipe
A technology for enhancing heat transfer and heat transfer tubes, which is applied in the direction of heat transfer modification, cleaning of rotating equipment, cleaning of heat transfer devices, etc. Complicated structure and other issues, to achieve the effect of reducing raw material consumption, improving performance and reducing friction
- Summary
- Abstract
- Description
- Claims
- Application Information
AI Technical Summary
Problems solved by technology
Method used
Image
Examples
Embodiment Construction
[0024] As shown in Figure 8, an embodiment of the self-cleaning low-flow resistance rotor in the heat transfer tube of the present invention, which includes a rotor, a support frame 8 and a connecting axis 11, and the support frame 8 is fixed on the heat transfer tube The two ends of the pipe 10 and the two ends of the connection axis 11 are respectively fixed on the support frame 8, and the several rotors are mounted on the connection axis 11 between the two support frames 8, and the rotors are composed of the hollow shaft 3 and the working surface. It is composed of scroll fins 2 in a spiral shape, and more than one scroll fins 2 are arranged on the hollow shaft 3, and each scroll fin 2 is inclined to the center line of the hollow shaft 3, and each A scroll fin 2 is evenly fixed on the outer surface of the hollow shaft 3 .
[0025] Each adjacent fin 2 rotates around the hollow shaft 3 as the center, and the space swept by it is connected back and forth.
[0026] As shown in...
PUM
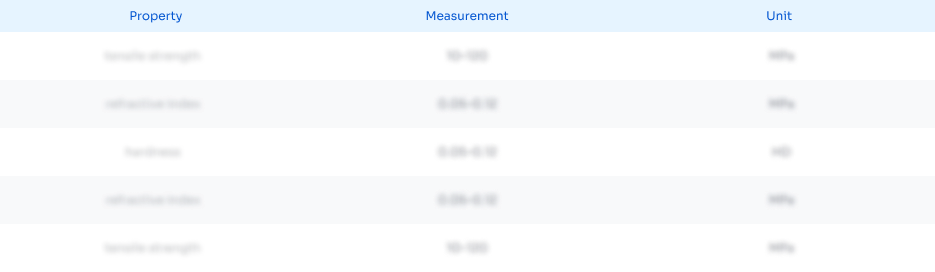
Abstract
Description
Claims
Application Information

- R&D
- Intellectual Property
- Life Sciences
- Materials
- Tech Scout
- Unparalleled Data Quality
- Higher Quality Content
- 60% Fewer Hallucinations
Browse by: Latest US Patents, China's latest patents, Technical Efficacy Thesaurus, Application Domain, Technology Topic, Popular Technical Reports.
© 2025 PatSnap. All rights reserved.Legal|Privacy policy|Modern Slavery Act Transparency Statement|Sitemap|About US| Contact US: help@patsnap.com