Method for calcination of chamotte in rotary cement kiln with coal gas as fuel
A cement rotary kiln and rotary kiln technology, applied in cement production, clinker production, rotary drum furnace, etc., can solve problems such as gas surplus, reduce gas emissions, reduce environmental pollution problems, and improve energy efficiency.
- Summary
- Abstract
- Description
- Claims
- Application Information
AI Technical Summary
Problems solved by technology
Method used
Image
Examples
Embodiment 1
[0030] Example 1: An equipment for calcining clinker in a cement rotary kiln using coal gas as fuel
[0031] This embodiment is shown in Figure 1, including: rotary kiln 5, five-stage cyclone tube 8, kiln tail smoke chamber 6, burner 4, cooler 9; The smoke chamber 6 communicates with the five-stage cyclone tube 8, and the kiln tail smoke chamber 6 is connected with the calciner 7; the kiln head of the rotary kiln 5 is provided with a burner 4, and the air inlet of the burner 4 is connected with a gas pipeline 1; the rotary kiln 5 The discharge end of the kiln head is provided with a clinker cooler 9. The gas pipeline 1 is connected with a flow control valve 3 and a gas regulator cabinet 2, the burner 4 is a gas burner, and the kiln tail smoke chamber 6 has slopes with angles of 55° and 45° connected in sequence.
[0032] The cooler 9 is connected with the kiln head 5, and is used for cooling the high-temperature clinker, and at the same time is responsible for heating the sec...
Embodiment 2
[0033] Example 2: A method for calcining clinker in a cement rotary kiln using coal gas as fuel
[0034] As shown in Figure 1, taking the 1000t / d new dry-process cement rotary kiln as fuel with coke oven gas as an example, the steps are as follows:
[0035] A. Transport the coke oven gas with large pressure fluctuations to the gas stabilizing cabinet 2 through the gas delivery pipeline 1, the gas stabilizes the pressure to 10KPa through the stabilizing cabinet 2, and adjusts the flow rate to 2.20-2.30Nm through the gas flow control valve 3 3 / s, the heat is equivalent to the gas flow rate of 40000~41000kJ / s, which is ignited by the burner 4 and sprayed into the 5 heads of the rotary kiln;
[0036]B. The raw meal after fully decomposing the carbonate in the production of new-type dry clinker is collected by the fifth-stage cyclone 8 of the five-stage cyclone 8, and sent through the fifth-stage cyclone 8 feeding pipe To the kiln tail smoke chamber 6, the raw material is buffere...
Embodiment 3
[0038] Example 3: A method for calcining clinker in a cement rotary kiln using coal gas as fuel
[0039] As shown in Figure 1, the steps are as follows:
[0040] A. The high-coke mixed gas with large pressure fluctuations is transported to the gas stabilizing cabinet 2 through the gas delivery pipeline 1. The gas stabilizes the pressure to 18KPa through the stabilizing cabinet 2, and adjusts the heat through the gas flow control valve 3 to be equivalent to 40000-41000kJ The gas flow rate of / s is ignited by the burner 4 and sprayed into the 5 heads of the rotary kiln;
[0041] B. The raw meal after fully decomposing the carbonate in the production of new-type dry clinker is collected by the fifth-stage cyclone 8 of the five-stage cyclone 8, and sent through the fifth-stage cyclone 8 feeding pipe To the kiln tail smoke chamber 6, the raw material is buffered into the tail of the rotary kiln 5 through the 55° and 45° slopes in the kiln tail smoke chamber 6, and under the action...
PUM
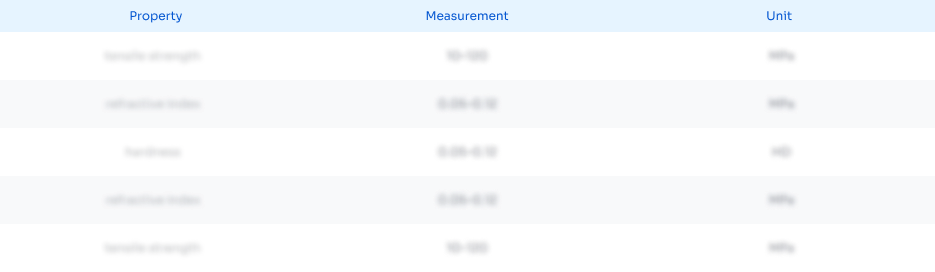
Abstract
Description
Claims
Application Information

- R&D
- Intellectual Property
- Life Sciences
- Materials
- Tech Scout
- Unparalleled Data Quality
- Higher Quality Content
- 60% Fewer Hallucinations
Browse by: Latest US Patents, China's latest patents, Technical Efficacy Thesaurus, Application Domain, Technology Topic, Popular Technical Reports.
© 2025 PatSnap. All rights reserved.Legal|Privacy policy|Modern Slavery Act Transparency Statement|Sitemap|About US| Contact US: help@patsnap.com