Method for producing nano crystalline stone materials
A production method and technology of microcrystalline stone, applied in glass production and other directions, can solve the problems of high probability of product defects, complicated production process, and reduced product qualification rate.
- Summary
- Abstract
- Description
- Claims
- Application Information
AI Technical Summary
Problems solved by technology
Method used
Examples
Embodiment 1
[0029] The production method of the nano crystallite material in the present embodiment 1, comprises the following steps:
[0030] 1) Molten glass: the raw materials used include the following components, and the weight percentage of each component is: SiO 2 55.7%, CaO 5.2%, MgO 7.3%, Al 2 o 3 6.2%, F 7.3%, Na 2 O 6%, K 2 O 6%, ZnO 2%, B 2 o 3 2%, P 2 o 5 1.5%, Sb 2 o 3 0.8%;
[0031] The raw materials are mixed according to the composition ratio, and then melted at a temperature of 1430°C. The melted molten glass should ensure the homogenization of the components, the uniformity of the temperature and the stability of the flow rate.
[0032] 2) Press the glass substrate: cool the molten glass to 1200°C, control the outflow of the glass liquid, and then press it through a calender to form a glass substrate.
[0033] 3) Carry out nucleation, crystallization, and annealing treatment: firstly perform nucleation treatment at 760°C for 20 minutes, then raise it to ...
Embodiment 2
[0041] The production method of the nano-microcrystalline stone material in the present embodiment 2, comprises the following steps:
[0042] 1) Molten glass: the raw materials used include the following components, and the weight percentage of each component is: SiO 2 51%, CaO 5.8%, MgO 8%, Al 2 o 3 7%, F 6.8%, Na 2 O 5%, K 2 O 7.8%, ZnO 1.5%, B 2 o 3 2.3%, P 2 o 5 1%, Sb 2 o 3 0.8%, MnO 2 1.5%, TiO 2 1.5%; the raw materials are mixed according to the composition ratio, and then melted at a temperature of 1410°C. The melted molten glass must ensure the homogenization of the components, the uniformity of the temperature and the stability of the flow rate.
[0043] 2) Press the glass substrate: cool the molten glass to 1300°C, control the outflow of the glass liquid, and then press it through a calender to form a glass substrate.
[0044] 3) Carry out nucleation, crystallization, and annealing treatment: first perform nucleation treatment at 755°C for 15 min...
Embodiment 3
[0052] The production method of the nano-microcrystalline stone material in the present embodiment 3, comprises the following steps:
[0053] 1) Molten glass: the raw materials used include the following components, and the weight percentage of each component is: SiO 2 65.8%, CaO 4.2%, MgO 6%, Al 2 o 3 5.3%, F 4.2%, Na 2 O 5%, K 2 O 4%, ZnO 0.8%, B 2 o 3 1%, P 2 o 5 1.8%, Sb 2 o 3 0.7%, Cr 2 o 3 1.2%; the raw materials are mixed according to the composition ratio, and then melted at a temperature of 1450°C. The melted molten glass must ensure the homogenization of the components, the uniformity of the temperature and the stability of the flow rate.
[0054] 2) Press the glass substrate: cool the molten glass to 1250°C, control the outflow of the glass liquid, and then press it through a calender to form a glass substrate.
[0055] 3) Carry out nucleation, crystallization and annealing treatment: first perform nucleation treatment at 760°C for 20 minutes, then...
PUM
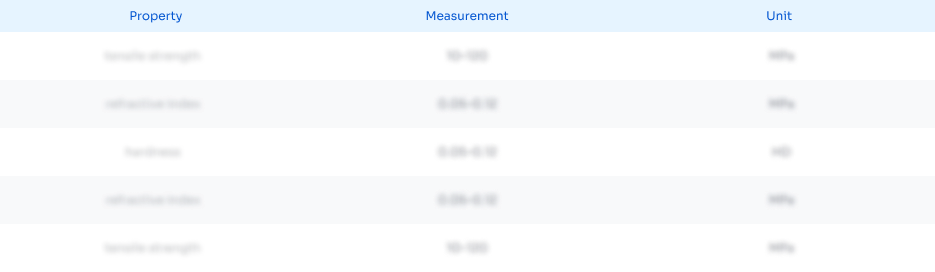
Abstract
Description
Claims
Application Information

- R&D
- Intellectual Property
- Life Sciences
- Materials
- Tech Scout
- Unparalleled Data Quality
- Higher Quality Content
- 60% Fewer Hallucinations
Browse by: Latest US Patents, China's latest patents, Technical Efficacy Thesaurus, Application Domain, Technology Topic, Popular Technical Reports.
© 2025 PatSnap. All rights reserved.Legal|Privacy policy|Modern Slavery Act Transparency Statement|Sitemap|About US| Contact US: help@patsnap.com