Extruding-bending integral forming method for magnesium alloy profiles
A magnesium alloy and profile technology, applied in metal extrusion, metal extrusion control equipment, metal processing equipment, etc., can solve problems such as large strain rate, serious die wear, and difficulty in ensuring the cross-sectional shape of bending parts. The effect of uniform transition and small deformation rate of section shape
- Summary
- Abstract
- Description
- Claims
- Application Information
AI Technical Summary
Problems solved by technology
Method used
Image
Examples
Embodiment 1
[0021] The grade of magnesium alloy used in this example is AZ31. The extruded profile is a round tube with a diameter of 42mm and a wall thickness of 4mm. The diameter of the three rollers is 150mm and the thickness is 50mm. The outer circumference has a semicircle with a radius of 21mm. The groove adopts the split extrusion method, the diameter of the original ingot is 100mm, the preheating temperature of the billet and the mold is 350°C, the holding time is 10 minutes, the extrusion speed is 50mm / s, and the pipe at the outlet of the extruder is The temperature is 310°C, and the temperature after bending deformation is 210°C; the surface of the formed pipe has no scratches, no cracks, no wrinkles, the bending radius of curvature is 200mm, the maximum wall thickness reduction rate is 8%, and the maximum ellipticity of the cross-section 7%.
Embodiment 2
[0023] In this example, AM30 magnesium alloy is used to make a plate with a width of 120mm and a thickness of 6mm. The diameter of the three rollers is 100mm and the thickness is 130mm. There is a rectangular groove with a width of 120mm and a depth of 2mm on the outside of the circumference of the rollers. The original The diameter of the ingot is 100mm, the billet and the corresponding extrusion die are preheated to 300°C in the resistance furnace, kept for 10 minutes, the extrusion speed is adjusted to 100mm / s, and the temperature of the plate at the outlet of the extruder is 340 °C, the temperature after bending deformation is 220 °C; after forming, the surface of the plate is smooth, there is no crack on the outer arc surface of the bend, no wrinkle on the inner arc surface, no change in the cross-sectional shape, and the final bending radius of curvature is 180mm.
Embodiment 3
[0025] In this example, AM50 magnesium alloy is used to make a bar with a diameter of 30mm. The diameter of the three rollers is 150mm and the thickness is 40mm. The outer circumference has an arc-shaped groove with a radius of 15mm. The diameter of the original ingot is 100mm. The corresponding extrusion dies are heated together with the furnace to 400°C, held for 10 minutes, the extrusion speed is adjusted to 10mm / s, the surface temperature of the bar at the outlet of the extruder is 350°C, and the temperature after bending deformation is 190°C The final formed bar has good surface quality, high dimensional accuracy, no cracks on the outside of the bend, no wrinkles on the inside of the bend, the maximum ellipticity of the cross-section is less than 2%, and the average radius of curvature of the bend is 150mm.
PUM
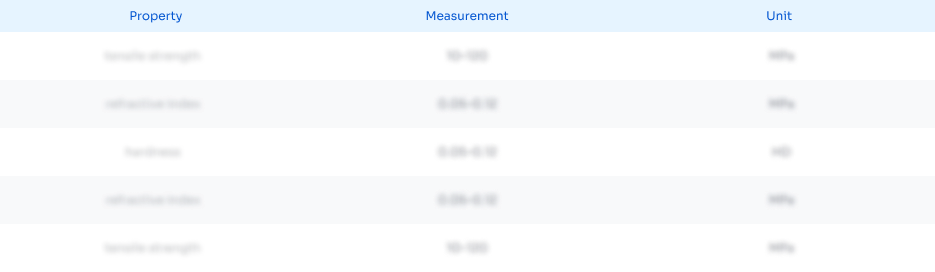
Abstract
Description
Claims
Application Information

- Generate Ideas
- Intellectual Property
- Life Sciences
- Materials
- Tech Scout
- Unparalleled Data Quality
- Higher Quality Content
- 60% Fewer Hallucinations
Browse by: Latest US Patents, China's latest patents, Technical Efficacy Thesaurus, Application Domain, Technology Topic, Popular Technical Reports.
© 2025 PatSnap. All rights reserved.Legal|Privacy policy|Modern Slavery Act Transparency Statement|Sitemap|About US| Contact US: help@patsnap.com