Method for producing pasteable polymers
A polymer and unsaturated technology, applied in the direction of chemical instruments and methods, chemical/physical processes, etc., can solve problems such as adverse effects on performance, and achieve the effect of avoiding complicated preparation and shortening the time of metering and adding
- Summary
- Abstract
- Description
- Claims
- Application Information
AI Technical Summary
Problems solved by technology
Method used
Image
Examples
Embodiment 1
[0049] 4400kg deionized water was added to the 15m3 stirred tank as an initial charge. Then add the following materials to it
[0050] 55kg alkyl aryl sulfonate
[0051] 55kg octadecyl monoethylene glycol ether
[0052] 5.5kg dimyristyl peroxydicarbonate
[0053] 5500kg vinyl chloride
[0054] The mixture was stirred at 25 °C for 15 min and then pressed through a rotor-stator-disperser with 10.5 bar and 0.5 mm gap width into 15 m 3 Stir in the kettle. The dispersion time here is 36min, and the throughput is 18m 3 / h.
[0055] The reaction mixture was heated in an autoclave to a polymerization temperature of 52°C. The polymerization time is about 8h.
[0056] After removal of the monomers, the dispersion is processed by means of spray drying to produce polyvinyl chloride powder. The spray-drying conditions are adjusted so that the particle size distribution of the powder meets the requirement of <1 wt% of particles larger than 63 μm.
[0057] To determine the rheologi...
Embodiment 2
[0059] 4400kg deionized water was added as an initial charge to the 15m 3 Stir in the kettle. Then add the following materials to it
[0060] 35kg alkyl aryl sulfonate
[0061] 35kg octadecyl monoglycol ether
[0062] 5.5kg dimyristyl peroxydicarbonate
[0063] 5500kg vinyl chloride
[0064] The mixture was stirred for 15 min at 25 °C and then pressed through a rotor-stator-disperser with 10.5 bar and 0.5 mm gap width into 15 m 3 Stir in the kettle. The dispersion time here is 36min, and the throughput is 18m 3 / h.
[0065] The reaction mixture was heated in an autoclave to a polymerization temperature of 52°C. The polymerization time is about 8h.
[0066] The dispersion was processed as in Example 1. The paste viscosities of the powders are reported in Table 1.
Embodiment 3
[0068] 4400kg deionized water was added as an initial charge to the 15m 3 Stir in the kettle. Then add the following materials to it
[0069] 35kg alkyl aryl sulfonate
[0070] 35kg octadecyl monoglycol ether
[0071] 5.5kg dimyristyl peroxydicarbonate
[0072] 3000kg vinyl chloride
[0073] The mixture was stirred for 15 min at 25 °C and then pressed through a rotor-stator-disperser with 10.5 bar and 0.5 mm gap width into 15 m 3 Stir in the kettle. The dispersion time here is 30min, and the throughput is 18m 3 / h. 2500 kg of vinyl chloride was fed into the stirred tank and the reaction mixture was subsequently heated.
[0074] The reaction mixture was heated in an autoclave to a polymerization temperature of 52°C. The polymerization time is about 8h.
[0075] The dispersion was processed as in Example 1. The paste viscosities of the powders are reported in Table 1.
PUM
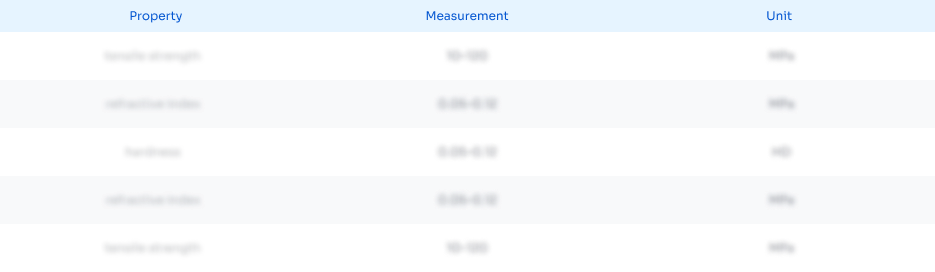
Abstract
Description
Claims
Application Information

- R&D
- Intellectual Property
- Life Sciences
- Materials
- Tech Scout
- Unparalleled Data Quality
- Higher Quality Content
- 60% Fewer Hallucinations
Browse by: Latest US Patents, China's latest patents, Technical Efficacy Thesaurus, Application Domain, Technology Topic, Popular Technical Reports.
© 2025 PatSnap. All rights reserved.Legal|Privacy policy|Modern Slavery Act Transparency Statement|Sitemap|About US| Contact US: help@patsnap.com