Preparation Method of Low-Cost Corrosion Inhibitor-Loaded Structure
A technology of loading structure and corrosion inhibitor, which is applied in the field of preparation of low-cost corrosion inhibitor loading structure, can solve the problems of complex preparation process, low production efficiency, and high process requirements, so as to avoid the preparation process, reduce the cost of raw materials, and avoid direct The effect of contact
- Summary
- Abstract
- Description
- Claims
- Application Information
AI Technical Summary
Problems solved by technology
Method used
Examples
Embodiment 1
[0022] (1) Under the stirring condition of 200r / min, in 100 parts by mass of water, add 0.1 mol / liter of hydrochloric acid to adjust the pH value of the solution between 3; then heat the solution to 50°C, add 10 parts by mass of cerium nitrate and mix well, Then add 1 mass part of absolute ethanol and stir for 0.5 hours;
[0023] (2) Add 10 parts by mass of analytically pure diatomaceous earth to the solution in step (1) under 500r / min stirring condition, and mix and stir for 3 hours;
[0024] (3) Centrifuge the mixture obtained in step (2), wash it with ethanol for 4 times, dry it in an oven at 80°C, take it out and grind it through a 200-mesh sieve to obtain a diatomite-loaded corrosion inhibitor structure.
[0025] How to use low-cost corrosion inhibitor-loaded structures:
[0026] Add 10 parts by mass of the diatomite-loaded corrosion inhibitor structure to 100 parts by mass of the water-based paint, and mix and stir for 3 hours.
Embodiment 2
[0028] (1) Under the stirring condition of 200r / min, in 100 parts by mass of water, add 0.1 mol / liter of hydrochloric acid to adjust the pH value of the solution between 4; then heat the solution to 50°C, add 12 parts by mass of cerium nitrate and mix evenly, Then add 1 mass part of absolute ethanol and stir for 0.5 hours;
[0029] (2) Add 10 parts by mass of analytically pure diatomaceous earth to the solution in step (1) under 500r / min stirring condition, and mix and stir for 3 hours;
[0030] (3) Centrifuge the mixture obtained in step (2), wash it with ethanol for 4 times, dry it in an oven at 80°C, take it out and grind it through a 200-mesh sieve to obtain a diatomite-loaded corrosion inhibitor structure.
[0031] How to use low-cost corrosion inhibitor-loaded structures:
[0032] Add 10 parts by mass of the diatomite-loaded corrosion inhibitor structure to 100 parts by mass of the water-based paint, and mix and stir for 3 hours.
Embodiment 3
[0034] (1) Under the stirring condition of 200r / min, in 100 parts by mass of water, add 0.1 mol / liter of hydrochloric acid to adjust the pH value of the solution between 5; then heat the solution to 50°C, add 15 parts by mass of cerium nitrate and mix evenly, Then add 1 mass part of absolute ethanol and stir for 0.5 hours;
[0035] (2) Add 10 parts by mass of analytical pure diatomaceous earth to the solution in step (1) under 500r / min stirring condition, and mix and stir for 3 hours;
[0036] (3) Centrifuge the mixture obtained in step (2), wash it with ethanol for 4 times, dry it in an oven at 80°C, take it out and grind it through a 200-mesh sieve to obtain a diatomite-loaded corrosion inhibitor structure.
[0037] How to use low-cost corrosion inhibitor-loaded structures:
[0038] Add 10 parts by mass of the diatomite-loaded corrosion inhibitor structure to 100 parts by mass of the water-based paint, and mix and stir for 3 hours.
PUM
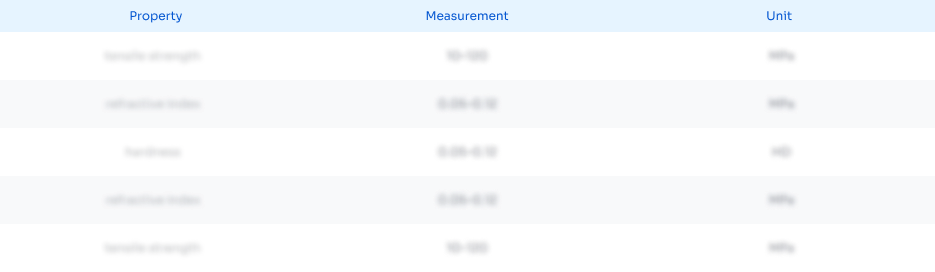
Abstract
Description
Claims
Application Information

- R&D
- Intellectual Property
- Life Sciences
- Materials
- Tech Scout
- Unparalleled Data Quality
- Higher Quality Content
- 60% Fewer Hallucinations
Browse by: Latest US Patents, China's latest patents, Technical Efficacy Thesaurus, Application Domain, Technology Topic, Popular Technical Reports.
© 2025 PatSnap. All rights reserved.Legal|Privacy policy|Modern Slavery Act Transparency Statement|Sitemap|About US| Contact US: help@patsnap.com