Method for producing lower-carbon olefin by fraction of coked diesel oil
A technology for coking diesel and low-carbon olefins, applied in cracking, petroleum industry, catalytic cracking, etc., can solve the problems of high equipment cost and operating cost, and achieve the effect of low investment cost and operating cost, simple process and flexible process plan
- Summary
- Abstract
- Description
- Claims
- Application Information
AI Technical Summary
Problems solved by technology
Method used
Examples
Embodiment 1
[0027] The raw material oil A mixed with hydrogen enters the hydrofinishing reaction zone, contacts with the hydrofinishing catalyst, and reacts under the same reaction conditions as in Comparative Example 1, and the reaction effluent is separated to obtain hydrocoked diesel oil. The hydrocoked diesel oil enters the atmospheric fractionation tower for fraction separation to obtain a light hydrocoked diesel fraction and a heavy hydrocoked diesel fraction, where the cut point between the heavy hydrocoked diesel fraction and the light hydrocoked diesel is 300°C. The atmospheric fractionation tower is a random packing tower, which adopts batch operation. The obtained heavy hydrocoked diesel fraction is used as raw material to enter the cracking furnace, and in the presence of water vapor, the steam cracking reaction is carried out under the same reaction conditions as in Comparative Example 1, and the reaction products are separated to obtain ethylene, propylene and butane Low ca...
Embodiment 2
[0033] The raw material oil B is mixed with hydrogen and enters the hydrofinishing reaction zone, contacts with the hydrofinishing catalyst, and reacts under the same reaction conditions as in Comparative Example 2, and the reaction effluent is separated to obtain hydrocoked diesel oil, and the obtained hydrofinishing The hydrocoked diesel oil enters the atmospheric fractionation tower for fraction separation to obtain a light hydrocoked diesel fraction and a heavy hydrocoked diesel fraction, where the cut point between the heavy hydrocoked diesel fraction and the light hydrocoked diesel is 310°C. The atmospheric fractionation tower is a random packing tower, which adopts batch operation. The obtained heavy hydrocoked diesel fraction is used as raw material to enter the cracking furnace, and in the presence of water vapor, the steam cracking reaction is carried out under the same reaction conditions as in Comparative Example 2, and the reaction products are separated to obtain...
Embodiment 3
[0039] The raw material oil C mixed with hydrogen enters the hydrofinishing reaction zone, contacts with the hydrofinishing catalyst, and reacts under the same reaction conditions as in Comparative Example 3, and the reaction effluent is separated to obtain hydrocoked diesel oil. The hydrocoked diesel oil enters the atmospheric fractionation tower for fraction separation to obtain a light hydrocoked diesel fraction and a heavy hydrocoked diesel fraction, where the cut point between the heavy hydrocoked diesel fraction and the light hydrocoked diesel is 280°C. The atmospheric fractionation tower is a random packing tower, which adopts batch operation. The obtained heavy hydrocoked diesel fraction is used as raw material to enter the cracking furnace, and steam cracking reaction is carried out in the presence of water vapor. After the reaction products are separated, low-carbon olefins such as ethylene, propylene and butadiene are obtained, and steam cracking The reaction condi...
PUM
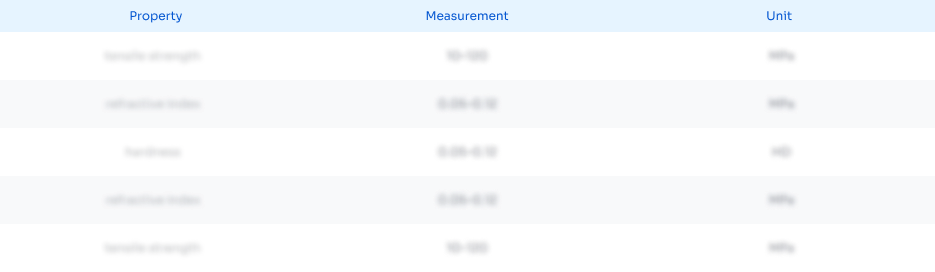
Abstract
Description
Claims
Application Information

- Generate Ideas
- Intellectual Property
- Life Sciences
- Materials
- Tech Scout
- Unparalleled Data Quality
- Higher Quality Content
- 60% Fewer Hallucinations
Browse by: Latest US Patents, China's latest patents, Technical Efficacy Thesaurus, Application Domain, Technology Topic, Popular Technical Reports.
© 2025 PatSnap. All rights reserved.Legal|Privacy policy|Modern Slavery Act Transparency Statement|Sitemap|About US| Contact US: help@patsnap.com